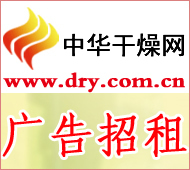
On January 8, 2011, Jiujiang Petrochemical completed the transformation of the MIP-CGP product optimization project for the 1 million tons/year FCC unit and successfully applied the Sinopec MIP-CGP technology with independent intellectual property rights. Improve the tube production rate optimization of complete sets of processes, external heat extraction and other advanced technologies.
At present, the light-liquid collection of the II set of catalytic cracking units has reached over 84%, which is 3-4 percentage points higher than before the transformation, the dry gas yield has dropped by 1 to 1.5 percentage points, the coke yield has dropped by 0.5 to 0.8 percentage points, and the energy consumption has been reduced. About 6 to 10 percentage points, the sulfur content is less than 150 ppm. Successfully solved the problem of gasoline olefin quality and increased the proportion of high-octane gasoline.
On September 20, 2011, Jiujiang Petrochemical conducted a 52-day, 1 million-ton/year I catalytic cracking unit stoppage overhaul and a MIP-CGP product yield optimization reform. Major projects include reactors, regenerators, settlers, external heat extractors, steam drums, renovation, distillation towers, absorption and stabilization towers, desorption towers, stability towers, re-absorption towers, and liquefied gas desulphurization towers. Material upgrading, fractionation and absorption Stable system heat transfer process optimization transformation, catalytic FSC instrument renovation, main fan and air compressor repair of large units. The reactor uses MIP technology and MIP-DCR technology to improve the tube production rate optimization technology, efficient and rapid sheet bed full regeneration technology and other 8 domestic and foreign advanced technologies. On November 11th, 2011, Jiujiang Petrochemical's catalytic cracking unit was successfully injected with fuel and realized a successful drive. At present, the I set of catalytic cracking unit operates stably, optimizes technical and economic indicators, and the energy consumption of equipment operation is greatly reduced. By adjusting the catalyst formulation, the light liquid recovery was increased from 79% before reformation to 84%, an increase of 5 percentage points, and the dry gas yield decreased by 1.09 percentage points; the catalyst was regenerated using a pre-burning can technology and successfully solved the original With the problem of unstable charring, the catalyst carbon content is reduced to 0.1% or less. The pressure drop of the flue gas line is reduced and the heat exchange process of the fractionation system is adjusted to reduce the system pressure drop and increase the energy utilization level. The energy consumption of the device is reduced by 10 to 15 kg of standard oil/ton.
C/Z/U Purline Roll Forming Machine
"C/Z/U Purlin Roll Forming Machine
C shape roll forming, Z shape roll forming machine and C&Z interchangeable roll forming machine. C purline, Z purline, H beam and others are used for big house building. They are the frame of the house. Normally speaking, the thickness of the material is between 1.5-3.0mm. So for the roll forming machine, it has high standard requirements." It can be widely used in the large and medium-sized enterprise civil construction, such as plant,warehouse,locomotive shed,hanger,exhibition,theatre,stadium and so on.
Purline Roll Forming Machine,Corrugated Roof Profile Machine,U Bracket Solar Power Stent Manufacturing System
Zhongtuo Roll Forming Machinery Co., ltd , https://www.frameforming.nl