The differential pressure transmitter is a transmitter that measures the pressure difference between the two ends of the transmitter and outputs a standard signal (such as 4~20mA, 0~5V). The difference between differential pressure transmitters and general pressure transmitters is that they have two pressure ports. Differential pressure transmitters are generally divided into positive pressure and negative pressure. Under normal circumstances, differential pressure transmitter positive pressure The pressure at the end should be greater than the pressure in the negative pressure section to measure.
Chinese name
Differential pressure transmitter
Foreign name
Differential pressure transmitter
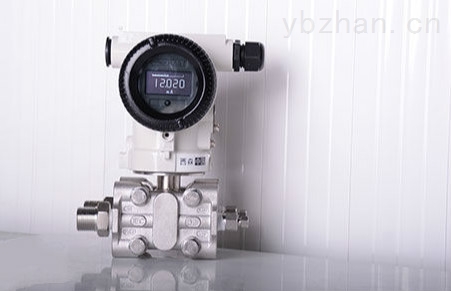
Differential pressure transmitters measure the level, density, and pressure of liquids, gases, and vapors, and then convert them into a 4- to 20-mA DC current signal output. The JT-3051DP can also communicate with each other via the BRAIN Communicator or the CENTUM CS/μXL or HART 275 Communicator, through which settings and monitoring can be performed. [1]
Analogâ— High precision
â— Range, zero external continuous adjustable
â— Good stability
â— Up to 500% positive migration and up to 600% negative migration
â— Two-wire system
â— Adjustable damping, over pressure resistance
â— Solid sensor design
â— No mechanical moving parts, less maintenance
â— Light weight (2.4kg)
â— All series of unified structure, strong interchangeability
â— Miniaturization (166mm total height)
â— Optional diaphragm material for contact with media
â— Unilateral overpressure
â— Low pressure cast aluminum alloy housing [2]
smartâ—Super measurement performance for pressure, differential pressure, level, flow measurement
â—Digital accuracy: +(-)0.05%
â— Analog Accuracy: +(-)0.75%+(-)0.1%FS
â— Full performance: +(-)0.25FS
â— Stability: 0.25% 60 months
â— Turndown ratio: 100:1
â— Measurement rate: 0.2S
â— Miniaturized (2.4kg) stainless steel flange for easy installation
â— The process connection is compatible with other products to achieve the best measurement
â— The only sensor (patented technology) using H alloy sheath in the world achieves excellent cold and thermal stability
â— Intelligent transmitter with 16-bit computer
Standard 4-20mA DC with digital signal based on HART protocol, remote control
â— Support upgrades to fieldbus and field-based control technology.
2 IntroductionThe differential pressure transmitter is used to prevent the medium in the pipeline from directly entering the transmitter, and the pressure-filled membrane and the transmitter are connected by a fluid-filled capillary. It is used to measure the level, flow and pressure of liquids, gases, or vapors, and then converts it into a 4-20 mA DC signal output. The cover for the domestic brand 3051 differential pressure transmitter.
Differential pressure transmitters are suitable for the following types of monitoring and control situations:
â— viscous medium at high temperature
â— Easy to crystallize media
â— Precipitating medium with solid particles or suspended solids
â—strongly corrosive or highly toxic media
It can eliminate the occurrence of leakage of pollution from the pressure guiding pipe. It can eliminate the tedious work of using the spacer fluid frequently because of instability of the measurement signal.
â— Continuously and accurately measure the interface and density
The remote transmission device can avoid cross-mixing of different mediums in time, so that the measurement result truly reflects the actual situation of the process change.
â— Occasionally high hygiene requirements
For example, in food, beverage and pharmaceutical industry production, it is not only required that the transmitter is in contact with the medium to meet the hygiene standards, but also that it is convenient for flushing to prevent cross-contamination of different media.
3 design principlesAs the name implies, the differential pressure transmitter measures the pressure difference, which is â–³P=ÏgΔh. Since the tank is often cylindrical, the area S of its cross-section circle is constant, then, gravity G = â–³ P · S = Ïg â–³ h · S, S unchanged, G and â–³ P is proportional to the relationship. That is, as long as the ΔP value is accurately detected, and inversely proportional to the height Δh, even if the oil volume expands or contracts when the temperature changes, the actual liquid level rises or falls, and the detected pressure remains unchanged. If the user needs to display the actual liquid level, media temperature compensation can also be introduced to resolve.
4 related parametersUse object: liquid, gas and steam
Measuring range: 0 ~ 0.1kPa to 0 ~ 40MPa
Output signal: 4 ~ 20mA DC (Specially available for four-wire 220V AC power supply, 0 ~ 10mA DC output)
Power supply: 12 ~ 45V DC, usually 24V DC
Load characteristics: related to the power supply, with a load capacity at a certain supply voltage shown in Figure 2, load impedance RL and power supply voltage Vs relationship: RL ≤ 50 (Vs a 12)
Indicator table: pointer linear indication 0 ~ 100% scale or LCD liquid crystal display.
Explosion-proof: Explosion-proof ExdIICT6
Range and Zero: External Continuously Adjustable
Positive and negative migration: the absolute value of the upper limit value and lower limit value of the range, measurement range after the zero point is undergoing positive or negative migration,
Do not exceed 100% of the upper limit of the measurement range. (Intelligent: Range ratio 15:1) The maximum positive migration is 500% of the minimum calibration range; the maximum negative migration is 600% of the minimum calibration range.
Temperature range: Amplifier operating temperature range: -29 ~ +93 °C (LT type: -25 ~ +70 °C).
Filling silicone oil measuring element: -40~+104°C
Flange type transmitter when filling high-temperature silicone oil: -20 ~ +315 °C, ordinary silicone oil: -40 ~ +149 °C
Static pressure: 4, 10, 25, 32MPa
Humidity: 5 to 95% relative humidity
Volume absorption: <0.16cm3
Damping (step response): When filled with silicone oil, it is generally adjustable between 0.2s and 1.67s.
Accuracy: ±0.2%
Dead zone: none (≤0.1%)
Stability: Absolute value of basic error that does not exceed the maximum range within six months (in smart year)
Vibration effect: In any axial direction, when the vibration frequency is 200Hz, the error is ±0.05%/g of the upper limit of the measurement range.
Power Influence: 0.005%/V less than output range
Load effect: If the power supply is stable, the load has no effect.
5 matters needing attention1. Do not apply more than 36V to the transmitter, resulting in damage to the transmitter.
2, do not touch the diaphragm with a hard object, resulting in damage to the isolation diaphragm;
3, the measured medium is not allowed to freeze, otherwise it will damage the sensor element isolation diaphragm, resulting in damage to the transmitter, if necessary, the transmitter temperature protection to prevent icing;
4. When measuring steam or other high-temperature medium, its temperature should not exceed the limit temperature when the transmitter is used, and the heat sink must be used above the temperature limit of the transmitter.
5. When measuring steam or other high-temperature medium, use a heat pipe to connect the transmitter and the pipe and use the pressure on the pipe to transfer to the transformer. When the measured medium is water vapor, appropriate amount of water should be injected into the heat pipe to prevent the superheated steam from directly contacting the transmitter and damaging the sensor.
6, in the pressure transmission process, should pay attention to the following points,
a, the transmitter and heat pipe connection, do not leak;
b. Before starting to use, if the valve is closed, the valve should be opened very carefully and slowly to prevent the measured medium from directly hitting the sensor diaphragm and damaging the sensor diaphragm.
c. The pipeline must be kept open. The deposits in the pipeline will pop up and damage the sensor diaphragm.
Failure analysis1. Investigation method:
Review the fire, smoke, odor, power supply changes, lightning strikes, humidity, misoperation, and mishandling before the failure.
2. Intuitive method:
Observe the external damage of the circuit, the leakage of the pressure guiding pipe, the overheating of the circuit, and the status of the power switch.
3. Test method:
1) Disconnection detection: Separate the suspected faulty part from other parts to see if the fault disappears. If it disappears, determine the fault location. Otherwise, you can proceed to the next step. For example: The smart differential pressure transmitter cannot work normally. , The power supply can be disconnected from the body, and the transmitter is powered on for communications by adding power to the site to see if the cable is overlaid with an electromagnetic signal of about 2 kHz to interfere with the communication.
2) Short-circuit detection: In the case of ensuring safety, the relevant part of the circuit is directly shorted, such as: the output value of the differential transmitter is too small, the pressure tube can be disconnected, and the differential pressure signal is directly from the pressure-receiving valve at one time. Directly lead to both sides of the differential pressure transmitter, observe the transmitter output, to determine the plugging and leakage connectivity of the pilot pressure pipeline.
3) Replacement test: Replace the part that is suspected of being faulty and determine the fault location. For example, if you suspect that the transmitter circuit board has failed, replace it temporarily to determine the cause.
4) Division detection: The measurement loop is divided into several parts, such as: power supply, signal output, signal transmission, signal detection, according to sub-section inspection, from the simple to the complex, from the table and in, narrow the scope, to identify the fault position.
Troubleshooting steps1. Check whether the differential pressure transmitter's power supply is reversed, and whether the positive and negative power supply is connected correctly.
2. Measure the power supply of the transmitter. Is there a 24V DC voltage? Ensure that the power supply voltage to the transmitter is ≥12V (ie, the voltage at the input of the transmitter power supply is ≥12V). If there is no power, check whether the circuit is broken, whether the instrument is selected wrongly (input impedance should be ≤ 250Ω) and so on.
3, if the pressure transmitter is with a header, you need to check whether the header is damaged (you can short the first two lines of the header, if the short circuit is normal, then the header is damaged), if the header is damaged, You need to change the header.
4. If there is a problem with the differential pressure transmitter, connect the current meter to the 24V power supply circuit to check if the current is normal. If it is normal, the transmitter is normal. At this time, check whether other instruments in the loop are normal.
5. If the power supply is connected to the transmitter power input, connect the power cable to the power port.
Fault detectionIn the detection of differential pressure transmitter failure should understand that the principle of differential pressure transmitter, in order to allow us to more easily and quickly identify the reasons.
The principle of differential pressure transmitter: differential pressure from the two side of the pressure tube directly on the transmitter diaphragm on both sides of the diaphragm, through the diaphragm of the sealing liquid conduction to the measuring element, the measuring element will be measured The differential pressure signal is converted to its corresponding electrical signal and passed to the converter. After amplification and other processing, it becomes the standard electrical signal output.
Several common and practical measurement methods for differential pressure transmitters:
1. In combination with the throttling element, the differential pressure value generated before and after the throttling element is used to measure the liquid flow.
2. Using the pressure difference generated by the liquid's own gravity, measure the height of the liquid.
3. Directly measure the pressure difference between different pipes and tanks.
In the measurement process of the transmitter, there are often some faults, and the timely determination and analysis of the faults are crucial to the ongoing production. Based on our experience in routine maintenance, we summarized some judgment analysis methods and analysis procedures.
On-site calibrationCalibration of a conventional differential pressure transmitter
First adjust the damping to the zero state, first adjust the zero point, then increase the pressure to full range, so that the output is 20mA. The adjustment in the field is fast. Here, introduce the zero and span quick adjustment method. Zero adjustment has almost no effect on fullness, but when fullness has an effect on the zero point, its effect is approximately 1/5 of the span adjustment without migration, ie 1mA of span is adjusted upwards and the zero point will move approximately 0.2mA upwards. ,vice versa. For example: input full-scale pressure is 100Kpa, the reading is 19.900mA, adjust the range potentiometer to make the output 19.900 + (20.000-19.900) × 1.25 = 20.025mA. When the range increases 0.125mA, the zero increases 1/5 × 0.125 =0.025. The zero point potentiometer makes the output 20.000mA. After the zero point and full scale are adjusted properly, check the middle scale again to see if it is out of tolerance and fine tune if necessary. Then perform the adjustment of the migration, linearity, and damping.
Smart differential pressure transmitter calibration
It is not possible to calibrate the smart transmitter using the above-mentioned conventional method because it is determined by the structural principle of the HART transmitter. Because the smart transmitter is between the input pressure source and the generated 4-20mA current signal, in addition to the mechanical and electrical circuits, there is also the microprocessor chip's operation of the input data, so the adjustment is different from the conventional method. Actually, the manufacturer's calibration of smart transmitters is also explained. For example, ABB's transmitters have calibration points such as "set range", "re-quantification range", and "fine adjustment". The "set range" operation is mainly through the digital setting of LRV and URV to complete the configuration work, while the "re-quantity range" operation requires that the transmitter is connected to a standard pressure source and guided by a series of instructions. The transmitter senses the actual pressure directly and sets the value. The initial and final setting of the range depends directly on the actual pressure input value. However, to see that although the analog output of the transmitter is correctly related to the input value used, the digital reading of the process value shows a slightly different value, which can be calibrated by a fine-tuning item. As each part needs to be adjusted separately and must be adjusted together, the following steps can be performed during actual calibration:
1. Do a 4-20mA trim once to correct the internal D/A converter. Since it does not involve sensing components, no external pressure signal source is required.
2. Do a full fine-tuning again, so that the 4-20mA, digital readout matches the actual applied pressure signal, thus requiring a pressure signal source.
3. Finally, a heavy quantification process was performed, and the analog output 4-20 mA was adjusted to match the applied pressure signal source. The effect was exactly the same as that of the zero (Z) and range (R) switches on the transmitter housing.
how to chooseThe differential pressure transmitter measures the pressure difference of the medium in the process pipe or tank, and converts the differential pressure value measured by the data into the current signal output through the data conversion. Selecting a differential pressure transmitter requires knowledge of the following parameters:
1, differential pressure value
2, medium
3, the working pressure of the medium
4, the working temperature of the medium
5, is smart or analog
Selection basis(1) Measurement range, required accuracy and measurement function;
(2) The environment facing the measuring instrument, such as the petrochemical industrial environment, has the potential for hot (toxic) and explosion hazardous atmospheres, high ambient temperatures, etc.;
(3) The physical and chemical properties and state of the measured medium, such as strong acid, strong alkali, viscous, easy solidification, crystallization, and vaporization;
(4) Changes in operating conditions, such as changes in medium temperature, pressure, and concentration. Sometimes it is also necessary to take into account the changes in gas phase and liquid phase concentrations and densities from start-up until the parameters reach normal production;
(5) The structure, shape and size of the container to be measured, the accessories of the equipment inside the container, and the mouths of various import and export materials shall be considered, such as towers, solution tanks, reactors, boiler steam drums, vertical tanks, spherical tanks, etc.;
(6) Other requirements, such as environmental protection and health requirements;
(7) There should be a unified consideration for engineering instrument selection, and it is required to reduce the variety of specifications as much as possible and reduce spare parts in order to facilitate management;
(8) Actual process conditions:
1 depends on the physical and chemical properties of the medium and the degree of cleanliness, the preferred conventional differential pressure transmitter and buoyancy level transmitter, but also to contact the media part of the material selection;
2 Single flange type differential pressure transmitter can be used for some suspended materials, foams and other media. Some easy-to-precipitate, easy-to-crystallize plug-in dual flange differential pressure transmitters;
3 Consider what kind of equipment the measured object belongs to. For tanks and tanks, the volume of the tank is small, the scope of measurement is not too large, the volume of the tank is large, and the range of measurement may be large;
4 For the liquid level of high viscosity medium and the liquid level of the high pressure equipment, because the equipment can't open the hole, you can use RF level meter to measure;
5 In addition to measurement methods and technical problems, there are instrument investment issues.
6 practical applicationsIn Wenzhou New Century Oil Storage Project, the author applies this idea to the actual design.
Design conditions: 2000m3 oil tank, diameter d = 14.5m, height can get the actual oil product inventory G, from the formula also know its density Ïh = 14m.
A table: Flange-type explosion-proof differential pressure transmitter, flange type is used to prevent sedimentation of the bottom of the tank and block the pressure tube, the transmitter range 0 ~ 140kPa.
Two-time table: Uses the intelligent light column to display the alarm meter, the universal signal input, may change the measuring range arbitrarily, uses the light column to demonstrate the liquid level, uses the number to display the tonnage of the oil product. Taking a 6# tank as an example, S=π×r2=3.14×7.252=165m2 and the height is 14m.
At the top of the tank, the differential pressure transmitter is designed with a liquid level alarm as a double fuse. In the application, since the measured value is directly the tonnage, the oil tank can be stored regardless of the type of oil. The value displayed in the secondary table is the tonnage of the oil in the tank, which avoids the need to measure the density for conversion.
Differential Pressure Transmitter In general, the oil is often pumped through the elliptical gear flow meter for metering and delivery. Because the accuracy of the flow meter is limited, the highest is only 0.2. The differential pressure transmitter also needs to measure the density, and the result is often Some in and out, causing measurement disputes. Because the result of the tank measurement is tons, and the precision can reach 0.2 or even 0.1, compared with the positive displacement flowmeter, the differential pressure transmitter measurement result is more accurate. Although the absolute error of the measurement result is relatively large due to the resolution when a small amount of oil is exported to and out of the warehouse, the higher precision and the smaller relative error, the differential pressure, when a large number of oils enter and exit the warehouse. Transmitters are unmatched by other means of measurement and are particularly suitable for monthly, quarterly and annual inventory. Practice has shown that its main advantages are: 1 simple and convenient installation and maintenance; 2 intuitive and clear readings directly read the inventory of oil products; 3 exemption from the determination of density and conversion.
7 Oil depot metering(1) Design and installation should take into account that the pressure at the bottom of the tank should be lowered as much as possible to eliminate errors caused by temperature changes, and temperature compensation should be introduced if necessary.
(2) In the case where the horizontal section of the tank of the oil tank is not equal (as small as above), compensation measures should be considered.
(3) In order to achieve a certain accuracy, if there is a breather valve at the top of the tank, a differential pressure transmitter must be used instead of a pressure transmitter. When open tanks or precision requirements are not high, pressure transmitters can be used directly to facilitate installation.
(4) As far as possible, the secondary meter uses a smart meter, which can easily change the range and achieve temperature compensation.
8 product modelDifferential pressure transmitter type
1, smart differential pressure transmitter
2, high static differential pressure transmitter
3, micro differential pressure transmitter
4, remote differential pressure transmitter
1. Japan will develop a space sensor for missile warning. People's Network [reference date 2. USA developed inexpensive graphene sponge sensor. People's Daily [reference date
Classifying Screening Classifier
High Capacity and High Effective Mineral Classifier
Customized Spiral Classifier for Sand Gravel Separation
ISO/Ce Approved Fg750 Series Spiral Screw Classifier for Iron Mining/Classifying Gravity/Liquid
Mining Washer Machine Spiral Classifier for Sale Africa,South Africa,Kenya,Cameroon,Congo,Nigeria Africa countries
Gold Mining Classifying Equipment Gold Ore Classifier Ball Milling Machine Spiral Classifier for Sale
Mineral Process Ore Desliming Double Screw Spiral Classifier
Silica Sand Washing Plant Sand Classifying Machine Spiral Classifier
Slurry Ore Classifier with Ball Mill for Gold Ore Processing
Technical Feature
1.High degree of automation and strong stability; The scope of application is wide.
2.There are four different types of the classifiers :high-weir single spiral,high-weir twin spiral,sunken single spiral and sunken twin spiral.
3.Frequent maintenance of the scoop is avoided and wearing of the big and small gears is reduced.
4.Using materials and processing technology with excellent properties, ensure that the wear is mild and uniform, and prolong the service life.
5.Compared with other classifiers, the energy consumption is reduced by 50%.
6.High accuracy and high precision, completely eliminate the large particles and screen residue in the products;
7.It is convenient to maintain and operate, and greatly reduces maintenance.
Spiral Classifier,Screening Classifier,Spiral Sand Washer Machine,Mining Jaw Crusher Vibrating Feeder
Henan YK Prospecting Machinery Co., Ltd , https://www.yyundergrounddrillingrig.com