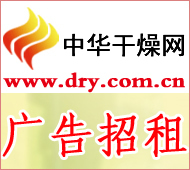
China Drying Newsletter With the successive announcement of 2012 annual results of listed companies in the photovoltaic industry, the operating difficulties of the entire photovoltaic industry have been exposed. Oriental Sunrise and Sunflower suffered a loss of over RMB 100 million. Chao Sun’s performance has changed dramatically. The entire photovoltaic industry chain has almost no exception. The upstream polysilicon industry not only has a serious overcapacity, but also faces multiple problems such as technology and energy consumption. The merger and reorganization of the industry is imminent.
According to statistics of the Photovoltaic Industry Association, as of the end of 2012, only 4 to 5 of the more than 60 polysilicon enterprises in China are producing a small amount of production, and more than 90% of the companies are already in production. This situation may be difficult in the short term. change.
Low comprehensive competitiveness
China is a major producer of photovoltaic cells and a major producer of polysilicon materials. At present, China has a total of more than 60 polysilicon production companies, such as full production at full capacity, annual production capacity to reach 385,000 tons, to meet the global demand for polysilicon photovoltaic companies. Even with an annual production capacity of 50%, it can measure 180,000 to 200,000 tons of polysilicon. Compared with the total domestic demand of about 100,000 tons in 2012, the supply exceeds demand.
While domestic production capacity is surplus, foreign polysilicon exacerbates low-price dumping, accelerating the domestic enterprises' plight. According to the forecast of the customs data in the first nine months of 2012, the import volume of the whole year may exceed 85,000 tons, an increase of 32% year-on-year. At the same time, due to the continuous increase in imported polysilicon, domestic polysilicon was suppressed by the low price of imports, and production once again declined. In the first half of 2012, the domestic polysilicon production was 38,000 tons; the annual output is expected to be about 60,000 tons, down 25% year-on-year.
China's polysilicon industry has inefficient production capacity and low overall competitiveness. At present, the average production cost of domestic enterprises is between US$40 and US$50 per kilogram. The production costs of domestic large-scale enterprises are mostly between US$30 and US$40 per kilogram, while the production costs of foreign advanced enterprises are below US$20 per kilogram. Foreign import prices were around US$20/kg, and a large amount of low-priced polysilicon was dumped into the domestic market, leading to an increase in imports from the domestic market share from 45% in 2011 to over 60% currently. These factors have exacerbated the difficulties of the domestic polysilicon enterprises, resulting in more than 90% of the enterprises are in the state of production suspension, and they may be forced to withdraw from the market.
Small capacity companies are facing bankruptcy
China's small-scale production capacity of polysilicon below 1,500 tons started in 2006 accounted for more than half. There are many unchangeable defects in the equipment configuration, the introduction of process technology, etc. due to the fact that there is no choice but to eat on the hungry.
In terms of equipment selection and configuration, due to the limitations of manufacturing technology at that time, most of the small-capacity polycrystalline silicon production enterprises used 9 pairs, 12 pairs, and 18 pairs of rod reduction furnaces from 2006 to 2010. There are small furnace types, low productivity, and energy consumption. Particularly high problems cannot be compared with the current 36-bar reduction furnaces, where the difference in power consumption is 50%. Hydrogen conversion technology that occupies an important part of the production process, the current cold hydrogenation technology than the original thermal hydrogenation, power consumption is about 30%, the conversion rate of 8% to 10%.
Therefore, at present, domestic small-capacity polysilicon enterprises generally have the “three highs and two lows†production characteristics of high equipment investment costs, high construction costs, high overall energy consumption, low production capacity, and low production rate. Although the production process also adopts the modified Siemens method, the process technology has not been optimized, resulting in a congenital deficiency in the development process of the enterprise and it is difficult to establish a foothold.
At present, the domestic polysilicon production enterprises with small production capacity have an overall polysilicon cost of about US$50/kg, and the current international polysilicon market price has dropped to US$17/kg, which is a serious production and sales inversion compared with the production cost.
Small-capacity polysilicon enterprises face multiple pressures due to their small scale, weak capacity release capacity and difficulty in cost reduction. Without scale advantages, technological advantages, and sustainable operation capabilities, they have no possibility of survival and development, and they can only walk. Liquidation reorganization or bankruptcy.
Industry mergers and acquisitions will accelerate
The State Council attaches great importance to the polysilicon industry. On December 19, 2012, Premier Wen Jiabao presided over the State Council executive meeting and confirmed to speed up the structural adjustment and technological progress of the photovoltaic industry, make good use of the market force mechanism, encourage enterprises to merge and reorganize, eliminate backward production capacity, and improve Technology and equipment levels to promote the healthy development of photovoltaic industry policy measures.
On January 7 this year, the National Energy Administration proposed at the 2013 national energy work conference that this year will vigorously develop distributed photovoltaic power generation, and the newly added photovoltaic power generation capacity will be 10 million kilowatts. These initiatives will bring hope for the photovoltaic industry, and industry mergers and acquisitions will also accelerate. It is expected that more than 1/3 or even 1/2 of the companies will be merged and reorganized.
In fact, as early as two years ago, the country had already paid attention to the problem of overcapacity in the photovoltaic industry. On December 31, 2010, the Ministry of Industry and Information Technology issued the "Polysilicon Industry Access Requirements" for the purpose of resolutely curbing the industry's redundant construction and overcapacity. Access conditions have made specific demands on the scale of polysilicon construction, as well as recycling and environmental protection. The regulations require that the solar-grade polysilicon project be larger than 3,000 tons per year, and the semiconductor-grade polysilicon project be greater than 1,000 tons per year. It also specifies specific indicators for resource recycling and energy consumption. It is also required that by the end of 2011, solar energy-grade polysilicon production lines with integrated power consumption greater than 200 kWh/kg be phased out.
In December 2011, the Ministry of Industry and Information Technology publicized the first batch of 20 polysilicon finalists that met the “Polysilicon Industry Access Requirementsâ€. Most other companies below 3,000 tons did not meet the access requirements and entered the bankruptcy merger.
In 2012, the total capacity of polysilicon enterprises exceeded 380,000 tons, of which 70% belong to a few first-tier manufacturers. First-line suppliers can meet all polysilicon needs. Most of the more than 50 second- and third-tier polysilicon manufacturers in China will withdraw from the market in the future, or wait for mergers and acquisitions.
• The produced parts are widely used in Auto Parts;Heat Sink;Agricultural,Marine;Architectural Machinery,Medica parts;Food Machinery, Valves,Bucket Tooth and so on.
We are OEM and specializing in:
1.Sand casting (Grey iron, ductile iron, aluminum,etc.)
2.Investment casting (carbon steel, stainless steel, alloy steel,etc.)
3.Die casting(aluminum, zinc, etc.)
4.Machinin(CNC Center, CNC lathe, lathe, drilling machine, milling machine, pressing machine, etc.)
Casting Parts Machining,Casting And Machining,Die Casting Parts,CNC Die Casting Parts
NINGBO CITY YINZHOU RUICAN MACHINERY CO.,LTD , https://www.ruican-machining.com