I. Introduction
In the realm of modern manufacturing, precision and efficiency are paramount. Among the myriad of tools available, two technologies stand out for their cutting prowess: laser cutting machines and CNC (Computer Numerical Control) machines. Both have revolutionized the way we approach cutting and shaping materials, but they do so in fundamentally different ways.
Laser-cutting machines utilize a highly focused laser beam to slice through materials with incredible accuracy. This method is particularly suited for intricate designs and thin materials, making it a favorite in industries such as aerospace, automotive, and electronics. On the other hand, CNC machines rely on computer programming to control a variety of tools, including drills, lathes, and milling machines. This versatility allows CNC machines to handle a wide range of materials and produce complex shapes, from detailed engravings to robust structural components.
Understanding the differences between these two technologies is crucial for businesses and hobbyists alike. Whether you are looking to invest in new equipment or simply curious about the latest advancements in manufacturing, this article will provide a comprehensive comparison of laser cutting machines and CNC machines. We will delve into their unique features, advantages, limitations, and practical applications to help you make an informed decision based on your specific needs.
II. What is a Laser Cutting Machine?
A laser cutting machine is a versatile and precise tool that uses a concentrated beam of light to cut through various materials. This technology works by directing the laser beam onto the surface of the material, causing it to heat up and either vaporize or melt away, creating a clean and accurate cut. The process is controlled by computer software, which allows for intricate designs and precise cuts that would be difficult to achieve with traditional cutting methods.
1. How Laser Cutting Works
Laser cutting involves several key components: the laser source, mirrors, lenses, and the cutting bed. The laser source generates a high-powered beam of light, which is then directed by mirrors and focused through lenses onto the material. The cutting bed moves the material in precise ways to achieve the desired cut pattern. The heat generated by the laser beam is sufficient to cut through materials such as metals, plastics, wood, fabric, and glass, depending on the power and type of laser used.
2. Types of Laser Cutting Machines
CO2 Lasers: These are the most common type of laser cutters. They use a gas mixture (primarily carbon dioxide) as the medium and are excellent for cutting non-metallic materials like wood, acrylic, and fabric. They can also cut thin metals.
Fiber Lasers: These solid-state lasers are more powerful and efficient than CO2 lasers. They excel at cutting metals, including reflective ones like copper and brass. Fiber lasers are known for their high speed and precision.
Crystal Lasers: Also known as Nd:YAG lasers, these use neodymium-doped crystals as the lasing medium. They are versatile and can cut both metals and non-metals, though they are less common in industrial applications.
3. Key Components of a Laser Cutting Machine
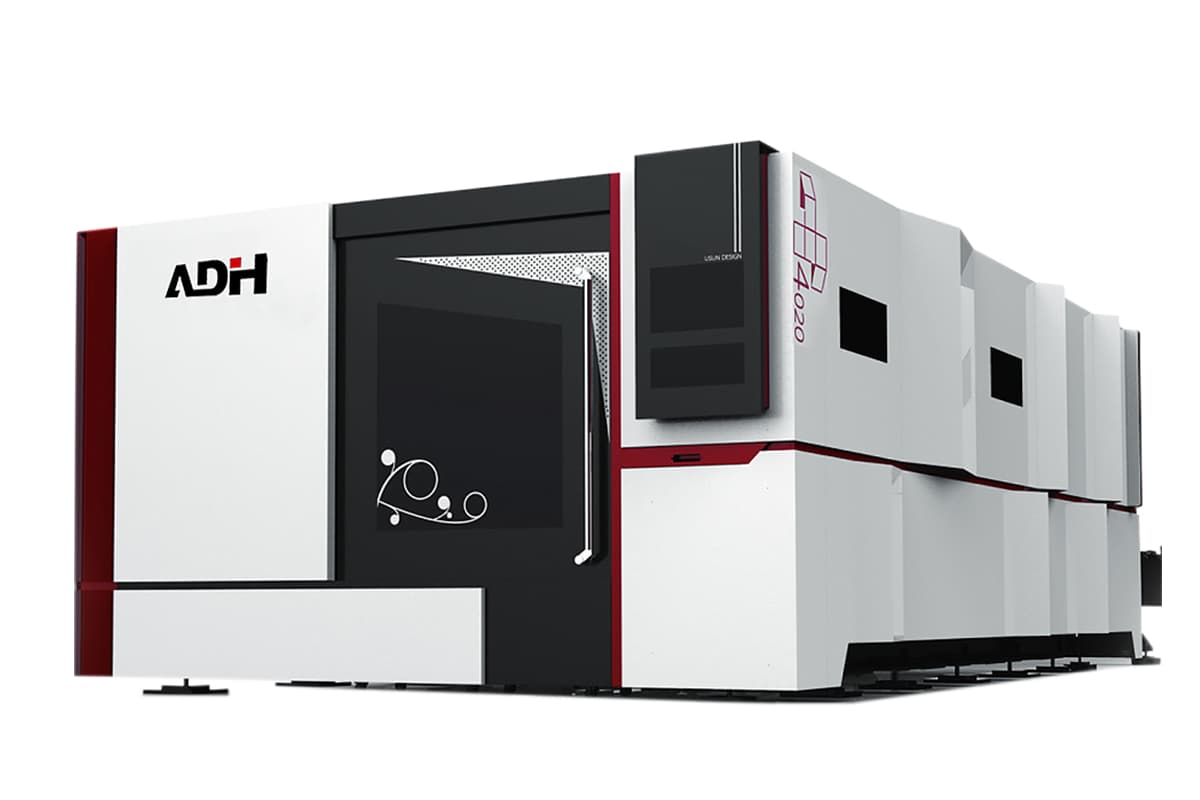
Laser Source: This generates the high-powered laser beam.
Beam Delivery System: Includes mirrors and lenses that direct and focus the laser beam onto the material.
CNC Control System: Computer software that controls the movement of the cutting head and the power of the laser.
Cutting Head: Houses the focusing lens and nozzle that directs the laser beam and assist gas onto the material.
Motion System: Typically includes a gantry system that moves the cutting head in X and Y directions.
Work Table: Supports the material being cut and often includes a honeycomb or slat design to minimize back reflections.
Exhaust System: Removes fumes, smoke, and small particles generated during the cutting process.
Cooling System: Maintains the optimal temperature of the laser source and other components.
4. Common Applications
Laser cutting machines are widely used in various industries due to their precision and versatility. Some common applications include:
- Aerospace: Cutting complex components for aircraft and spacecraft with high precision.
- Automotive: Manufacturing parts with intricate shapes and fine details.
- Electronics: Creating small, precise components for electronic devices.
- Jewelry Making: Producing detailed and intricate designs in metals and other materials.
- Signage and Art: Crafting detailed and customized signs, decorations, and art pieces.
5. Advantages of Laser Cutting Machines
- High Precision: The focused laser beam allows for extremely precise cuts, making it ideal for intricate and detailed designs.
- Non-Contact Cutting: Since the laser does not physically touch the material, there is minimal risk of distortion or damage.
- Fast Cutting Speeds: Laser cutting machines can cut through materials quickly, increasing production efficiency.
- Versatility: Capable of cutting a wide range of materials, including metals, plastics, wood, and more.
- Minimal Material Waste: The precision of the laser reduces the amount of material wasted during the cutting process.
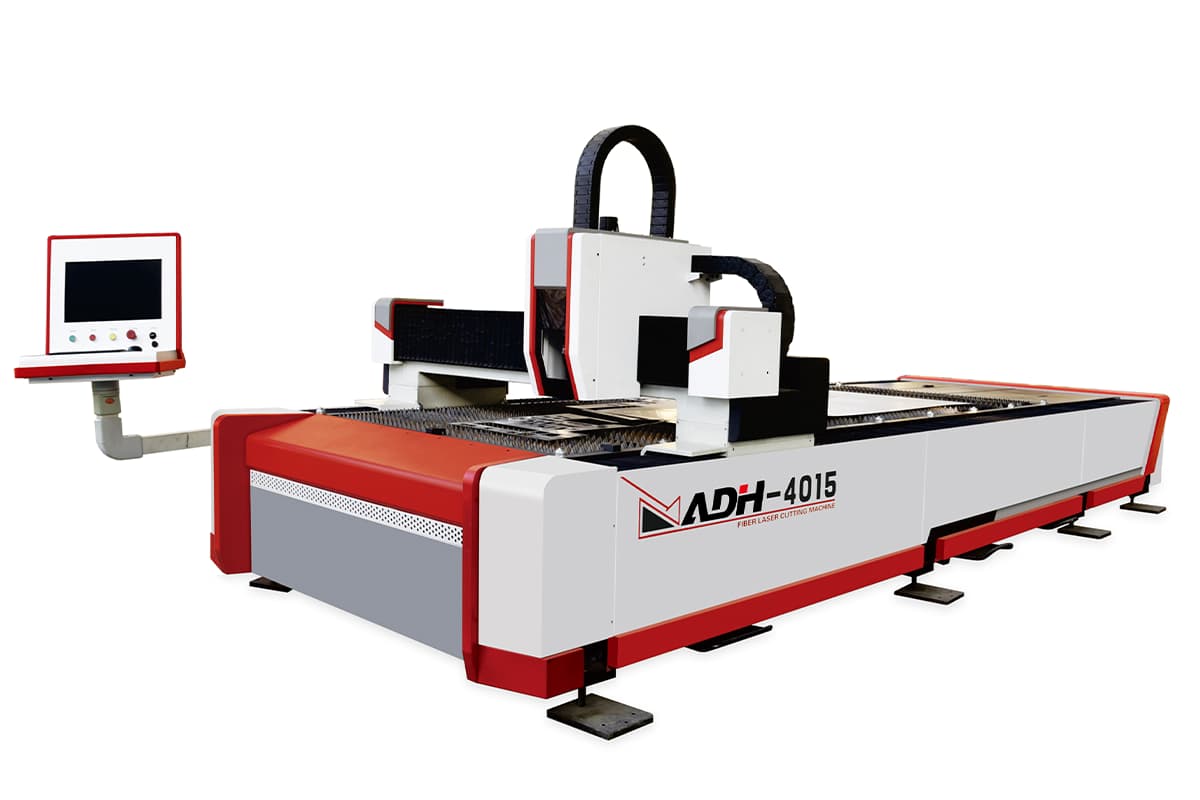
6. Limitations of Laser Cutting Machines
- Limited thick material cutting ability: Laser power may be insufficient for deep cutting
- Heat Affected Zone (HAZ): The heat generated by the laser can affect the material around the cut, potentially altering its properties or causing thermal damage.
- Maintenance and Calibration: Regular maintenance and calibration are necessary to keep the laser cutting machine operating at peak performance.
- Requires professional operation: Skilled technicians needed for operation and maintenance
- Harmful gases and fumes: Cutting certain materials may produce toxic gases, requiring ventilation systems
- High initial cost: Significant equipment investment required
III. What is a CNC Machine?
A CNC (Computer Numerical Control) machine is a highly versatile tool used in manufacturing to cut, shape, and engrave materials with precision. Unlike traditional manual machining, CNC machines are controlled by computer programs that dictate the movements of the cutting tools, ensuring consistency and accuracy in the manufacturing process.
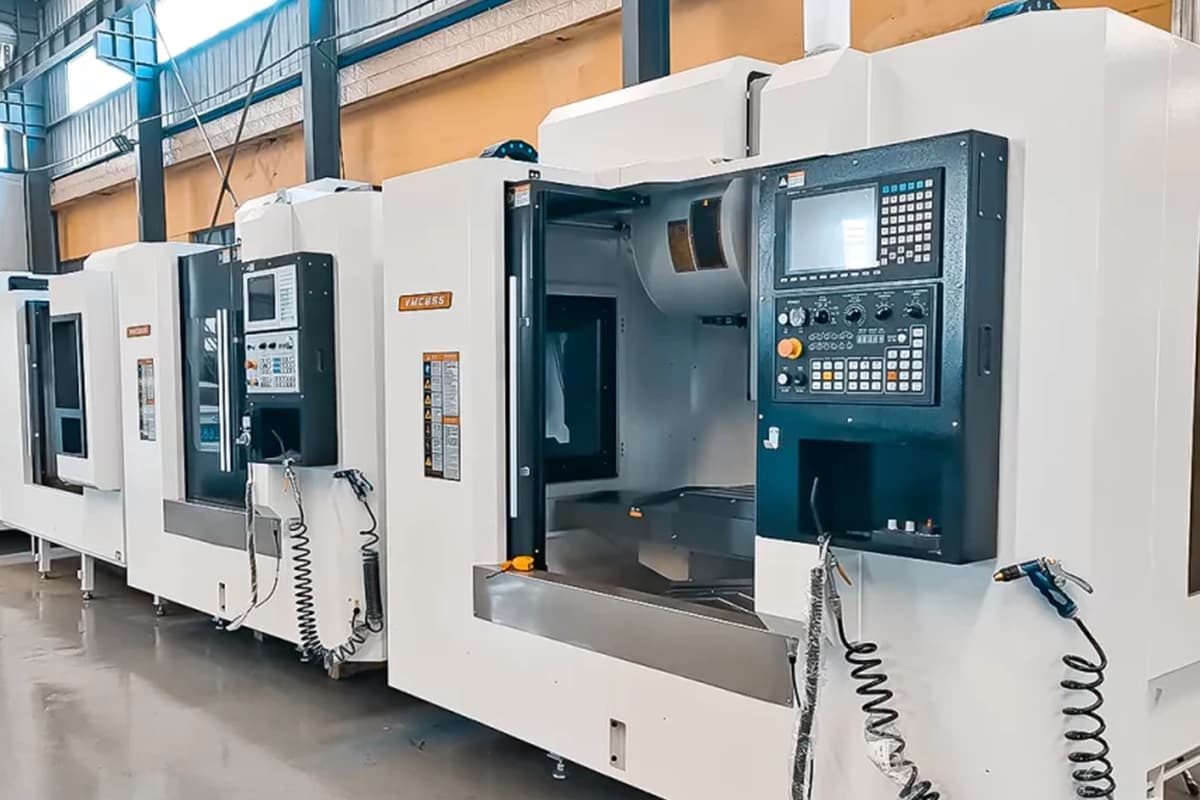
1. How CNC Cutting Works
CNC machines operate using a series of commands entered into a computer, which then controls the movements of the machine’s cutting tools. These commands are usually written in G-code, a language specifically designed for CNC programming. The machine follows these instructions to move the cutting tool along the X, Y, and Z axes, allowing for complex three-dimensional shapes to be created.
The cutting tools used in CNC machines can vary depending on the material and the type of cut required. Common tools include drills, lathes, and milling cutters. The machine can switch between different tools automatically, making it possible to perform multiple operations without manual intervention.
2. Types of CNC Machines
CNC Milling Machines: These versatile machines use rotating cutting tools to remove material from a workpiece. They can perform a wide range of operations, including face milling, end milling, and drilling.
CNC Routers: Similar to milling machines but typically designed for working with softer materials like wood, plastics, and composites. They excel at creating intricate designs and patterns.
CNC Plasma Cutters: These machines use a plasma torch to cut through conductive materials, primarily metals. They're known for their ability to cut thick materials quickly.
CNC Lathes: Used for creating cylindrical parts, lathes rotate the workpiece while a cutting tool removes material to achieve the desired shape.
CNC Grinders: These machines use abrasive wheels to achieve extremely fine finishes and tight tolerances on machined parts.
3. Key Components of a CNC Machine
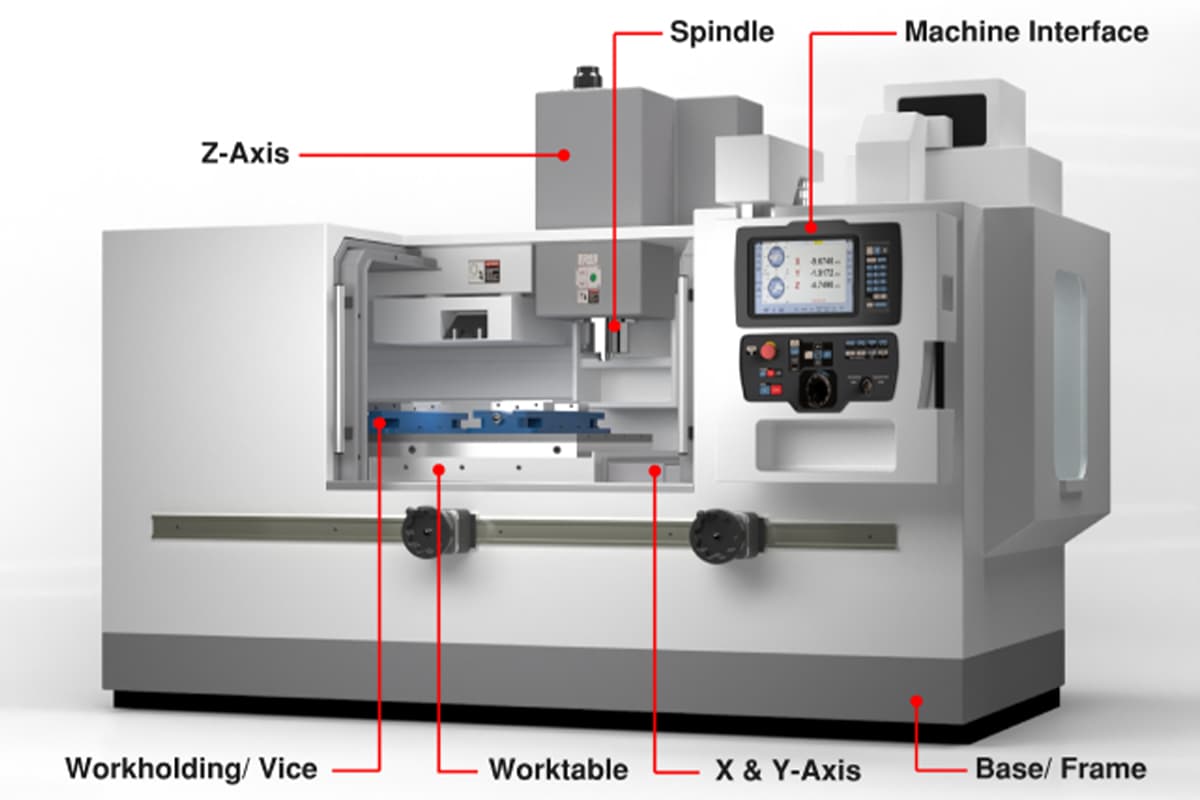
Machine Control Unit (MCU): The "brain" of the CNC machine, which interprets the G-code and controls the machine's movements and operations.
Drive System: Motors and mechanisms that move the cutting tools and/or workpiece according to the MCU's instructions.
Cutting Tools: Various interchangeable tools used for different operations (e.g., end mills, drill bits, grinding wheels).
Spindle: Rotates the cutting tool at high speeds.
Work Holding Devices: Clamps, vises, or other fixtures that securely hold the workpiece in place during machining.
Coolant System: Delivers coolant or cutting fluid to the cutting area to reduce heat and improve tool life.
Tool Changer: Automated system for switching between different cutting tools as needed.
Feedback Systems: Sensors and encoders that provide real-time information about the machine's position and performance.
User Interface: Typically a computer screen and control panel where operators can input commands and monitor the machining process.
4. Common Applications
CNC machines are used across a wide range of industries due to their flexibility and precision. Some common applications include:
- Automotive: Manufacturing engine components, transmission parts, and other critical vehicle elements.
- Aerospace: Creating high-precision parts for aircraft and spacecraft, often from hard-to-machine materials.
- Furniture Making: Cutting and shaping wood for custom furniture designs.
- Medical Devices: Producing complex and precise components for medical equipment and implants.
- Prototyping: Quickly creating prototypes for new products to test and refine designs before full-scale production.
5. Advantages of CNC Machines
- Versatility: CNC machines can work with a wide range of materials, including metals, plastics, wood, and composites.
- High Accuracy and Repeatability: Once a program is set up, CNC machines can produce identical parts with high precision, minimizing human error.
- Increased Productivity: CNC machines can operate continuously, increasing production speed and efficiency.
- Flexibility: Easily adjustable programming allows for quick changes in design and production processes.
- Complex Shapes and Designs: Capable of producing intricate three-dimensional shapes that would be difficult or impossible to create manually.
6. Limitations of CNC Machines
- Complex Programming: Writing and debugging CNC programs can be time-consuming and requires specialized knowledge.
- Material Limitations: While versatile, there are some materials that CNC machines may not handle well, such as very brittle or very soft materials.
- Initial Cost: The upfront cost of purchasing a CNC machine can be high, making it a significant investment for small businesses.
- Maintenance and Calibration: CNC machines require regular maintenance and calibration to ensure they continue to operate accurately and efficiently.
IV. Key Differences Between Laser Cutting and CNC Machines
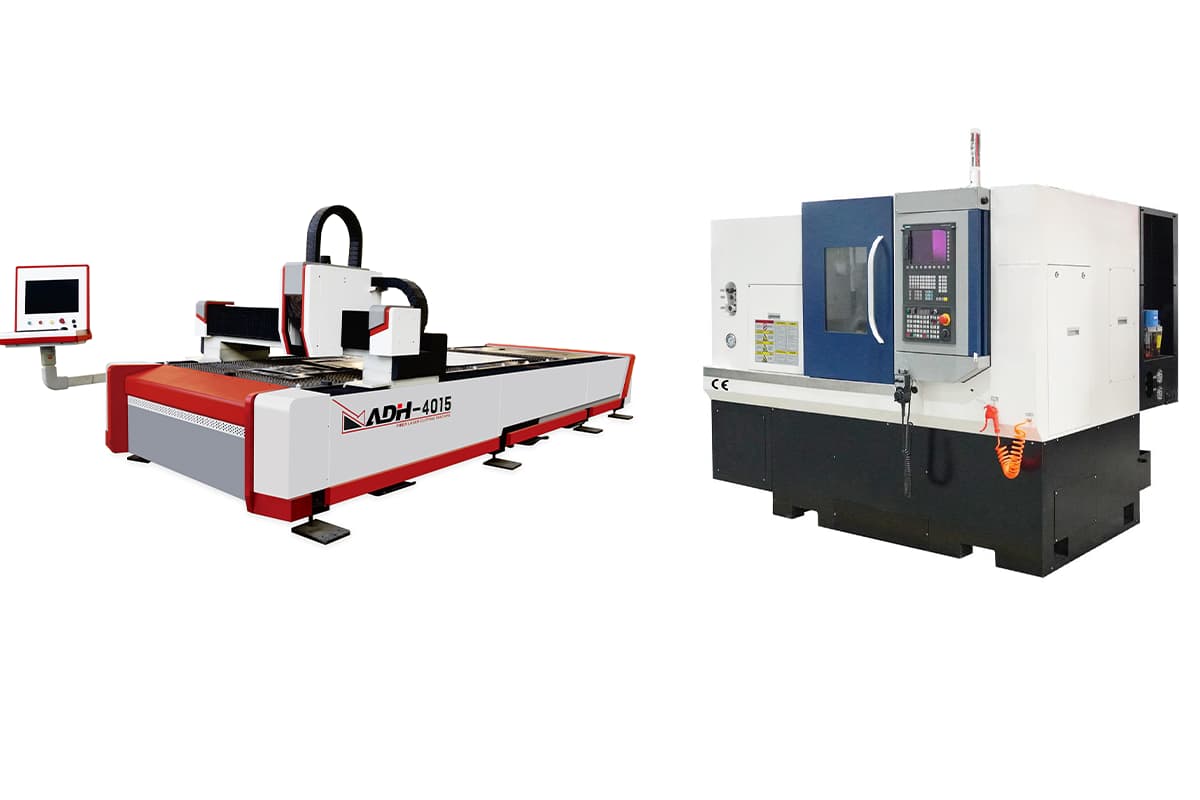
When deciding between a laser cutting machine and a CNC machine, it’s crucial to understand the key differences between the two technologies. These differences will help you determine which tool is best suited for your specific needs.
1. Precision and Detail
- Laser Cutting: Laser cutting machines are known for their high precision and ability to produce intricate designs. The focused laser beam allows for fine detail and minimal material waste, making them ideal for projects requiring intricate patterns or detailed cuts.
- CNC: While CNC machines also offer high precision, their accuracy is determined by the size of the cutting tool. CNC machines are better suited for producing complex three-dimensional shapes and can handle a broader range of materials with varying thicknesses.
2. Speed and Efficiency
- Laser Cutting: Laser cutting machines generally operate at faster speeds, especially when cutting thin materials and 2D designs. The non-contact cutting method reduces the time needed for material handling, making laser cutters more efficient for high-volume production.
- CNC: CNC machines are highly efficient for cutting thicker materials and complex 3D parts. Although the setup process for CNC machines can be more time-consuming, once configured, they can operate continuously, making them suitable for large-scale manufacturing.
3. Cost and Maintenance
- Laser Cutting: The initial cost of laser cutting machines can be higher, and they require regular calibration and cleaning to maintain performance. However, they offer lower operational costs due to minimal material waste.
- CNC: CNC machines typically have a lower initial cost but may incur higher maintenance expenses due to the numerous moving parts. Regular maintenance and calibration are necessary to ensure consistent accuracy and performance.
4. Material Compatibility
- Laser Cutting: Laser cutters are versatile and can handle a wide variety of materials, including metals, plastics, wood, fabric, and glass. However, they may struggle with thicker materials and are not suitable for all types of metals.
- CNC: CNC machines can work with a broader range of materials, including metals, plastics, wood, and composites. They excel at cutting thicker materials and creating complex three-dimensional shapes.
5. Advantages and Limitations
- Laser Cutting Machines
- Advantages: High precision, non-contact cutting, fast speeds, minimal material waste.
- Limitations: Less effective for thick materials, heat-affected zone (HAZ), requires regular maintenance.
- CNC Machines
- Advantages: Versatility, high accuracy, repeatability, cost efficiency, suitable for thicker materials.
- Limitations: Complex programming, material limitations, higher maintenance needs.
6. Practical Considerations
When choosing between laser cutting and CNC machines, consider the following practical aspects:
- Project Requirements: Evaluate the specific needs of your project, including material type, thickness, and design complexity.
- Cost Considerations: Factor in the initial investment, operational costs, and maintenance expenses.
- Production Speed: Consider the efficiency and speed required for your production processes.
- Industry Applications: Identify which technology aligns best with your industry and specific use cases.
7. Comparison Table
Comparison Item | Laser Cutting | CNC Machining |
Material Compatibility | Excels with thin to medium-thickness materials; Ideal for cutting plastics, wood, acrylic, fabric, paper, and some metals; CO2 lasers work best with non-metals, while fiber lasers are superior for metals; Limited effectiveness with reflective materials like copper or brass; Cannot cut materials that are too thick or heat-sensitive | Versatile across a wide range of materials, including metals, plastics, wood, and composites; Can work with thicker materials than laser cutting; Effective with hard metals like steel and titanium; Can machine materials that are heat-sensitive or reflective; Some limitations with very soft or flexible materials |
Precision and Accuracy | Extremely high precision, capable of intricate designs and fine details; Typical tolerance ranges from ±0.1mm to ±0.05mm; No tool wear, ensuring consistent accuracy over time; Beam width (kerf) is very narrow, allowing for tight tolerances | High precision, but generally not as fine as laser cutting for intricate 2D designs; Typical tolerance ranges from ±0.025mm to ±0.125mm, depending on the machine and material; Can achieve very smooth surface finishes; Precision can be affected by tool wear over time; Excels in creating precise 3D shapes and features |
Speed and Efficiency | Very fast for thin materials and 2D designs; No tool changes required, reducing downtime; Quick setup times; Efficient for large batch; productions of similar parts | Speed varies greatly depending on the complexity of the part and material hardness; Tool changes and setup can be time-consuming; Generally slower for simple 2D cuts compared to laser cutting; More efficient for complex 3D parts or when multiple operations are required on a single part |
Cost Considerations | Higher initial investment for the machine; Lower operating costs due to fewer consumables; Energy-efficient, especially fiber lasers; Cost-effective for large batches of thin, flat parts | Initial investment varies widely depending on the type and capabilities of the machine; Higher operating costs due to tool wear and replacement; More energy-intensive, especially when machining hard materials; More cost-effective for small batches of complex parts or when working with thick materials |
Versatility and Applications | Ideal for signage, decorative items, prototypes, and thin sheet metal parts; Excellent for industries like automotive, aerospace, electronics, and fashion; Limited to 2D cutting and engraving, with some 3D capabilities in specialized machines | Versatile for creating complex 3D parts, molds, and tools; Widely used in automotive, aerospace, medical, and general manufacturing industries; Can perform multiple operations like cutting, drilling, and milling in a single setup; Suitable for both prototyping and mass production |
Learning Curve and Ease of Use | Generally easier to learn and operate; Software interfaces are often more user-friendly; Less complex setup and maintenance procedures; Safer operation due to enclosed cutting area | Steeper learning curve, requiring an understanding of tooling, speeds, and feeds; More complex programming, especially for 3D parts; Requires more skill for setup, operation, and maintenance; Safety considerations due to exposed cutting tools and moving parts |
V. FAQs
1. What is better, laser cutting or CNC?
The answer to this question depends largely on the specific requirements of the project. Laser cutting is generally better for projects requiring high precision and intricate designs, especially with thin materials. It offers cleaner cuts and faster processing for detailed work. On the other hand, CNC machines are better suited for cutting thicker materials and creating complex three-dimensional shapes. They offer versatility in material compatibility and are ideal for projects requiring robust and intricate parts.
2. Can laser cutters cut metal?
Yes, laser cutters can cut metal, but their effectiveness depends on the type and thickness of the metal as well as the power of the laser. CO2 lasers are commonly used for cutting non-metallic materials and metals like steel, stainless steel, and aluminum, but they may struggle with thicker metals. Fiber lasers are more efficient for cutting metals, including reflective materials like brass and copper. However, for very thick metals, CNC machines might be more effective.
3. What materials can CNC machines cut?
CNC machines are highly versatile and can cut a wide range of materials, including:
- Metals: Steel, aluminum, brass, copper, and more.
- Plastics: Acrylic, PVC, polycarbonate, and various other types of plastic.
- Wood: Hardwood, softwood, plywood, MDF, and other wood types.
- Composites: Carbon fiber, fiberglass, and other composite materials.
- Foam: Various types of foam used in packaging, insulation, and other applications.
4. How accurate are laser cutting machines compared to CNC machines?
Laser cutting machines are known for their high precision and accuracy, often achieving tolerances as tight as 0.1 mm or better. This makes them ideal for intricate and detailed cuts. CNC machines also offer high accuracy, especially when well-maintained and properly programmed, but their precision can be limited by the size of the cutting tool and the complexity of the operation. Generally, for very fine and detailed work, laser cutting machines may provide better accuracy, while CNC machines excel in versatility and the ability to handle thicker materials.
VI. Conclusion
In the realm of modern manufacturing, laser cutting machines and CNC machines each have their unique strengths. Laser cutting machines excel in precision and speed, making them ideal for intricate designs and thin materials. On the other hand, CNC machines offer versatility and the ability to handle thicker materials, producing complex three-dimensional shapes. Understanding these differences is crucial for making informed decisions about which technology best suits your needs.
If you're looking for top-notch sheet metal production solutions, ADH Machine Tool is your go-to partner. With over 20 years of experience in manufacturing laser cutting machines, we are committed to providing the most advanced and reliable equipment. Contact us today to learn more about our products and see how we can help you enhance your production efficiency. Visit our website or call our customer service hotline to start your journey towards manufacturing excellence!
Low Tooth Number Cycloidal Gear,Metal Cycloidal Gear,Inner Gear Oil Pump,Semi-Imersed Gear Oil Pump
NINGBO JIECHENG ELECTROMECHANICAL CO.,LTD. , https://www.jiechengmechanical.com