The structure of the screw conveyor, mainly by the drive device, discharge hole, rotating screw axis, bearings, housing and feeding port, etc. Usually screw conveyor has the bearing on the material movement terminal side, it can withstand the material to spiral axial force of the blade. When the conveyor is longer than the fuselage, it should be added the middle hanging bearing.
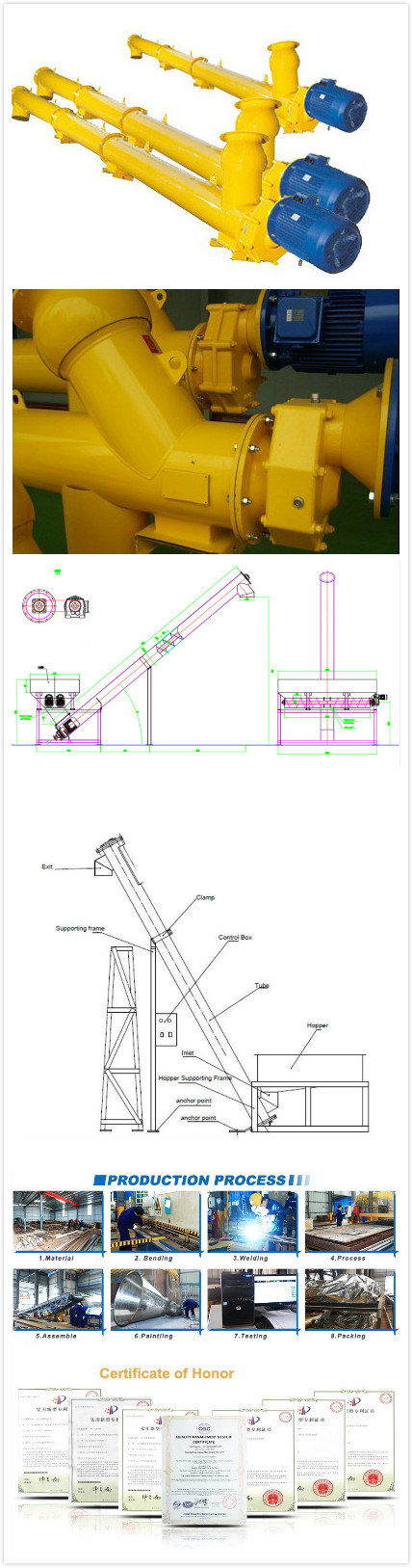
Characteristic:
Industrial cement screw conveyor with silo
1. Efficient delivery : small diameter , high rotating speed, large transmission capacity, variable pitch of spiral body, and small resistance of intermediate bearing make loading material smoothly, quickly and evenly.
 2. Random arrangement : conveyor has good integral rigidity and can transport the products flatly or steeply inclined, it can be connected with its corollary equipments directly , and can be set up and dismantled easily with small floor space.
 3. Good lubrication : low oil lubricating sliding tile, multilayer labyrinth oil seal design and integral lubricating system composed of of oil pump, distributor and pipeline are convenient and can completely lubricate all the running parts.Â
 4. Reliable sealing : the dust cover of reducer is reliable for preventing leakage which can protect reducer and create good working condition. Improved peephole can prevent water seepage and material leakage.
5. Diverse connection : feed inlet and outlet can be connected not only with universal ball, bag,flange etc but also butterfly valve and gate valve.Â
 6. Innovative design: special reducer designed and produced with introduced technology not only has the advantages of a small size, a big bearing torque.
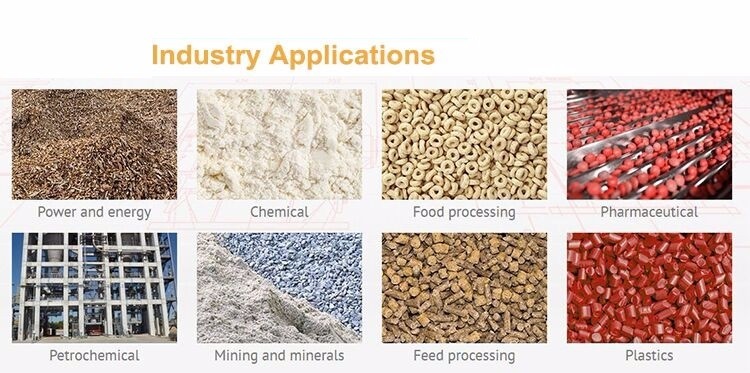
Product Features:
1. High-quality steel pipe with good integral rigidity;
2. Once-forming spiral double pitch paddles, which will never block the material;
3. Universal ball joint, which facilitates installation, adjustment and steering;
4. Double-pitch paddles, which decrease the compressed degree of material when being transported;
5. Standard parts and components, which make it is convenient for transportation;
6. High-quality reducer with heavy-duty design, large torque and low noise;
7. High-quality middle-hoisting bearing and tail bearing.
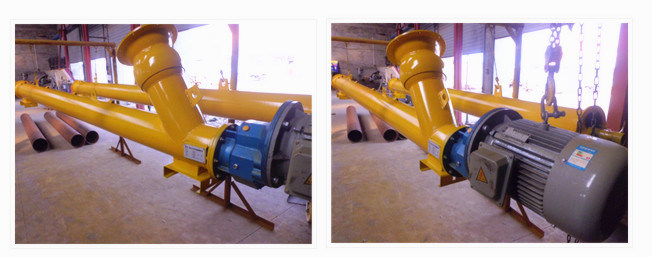
Product Structure:
The structure of the screw conveyor, mainly by the drive device, discharge hole, rotating screw axis, bearings, housing and feeding port, etc. Usually screw conveyor has the bearing on the material movement terminal side, it can withstand the material to spiral axial force of the blade. When the conveyor is longer than the fuselage, it should be added the middle hanging bearing.
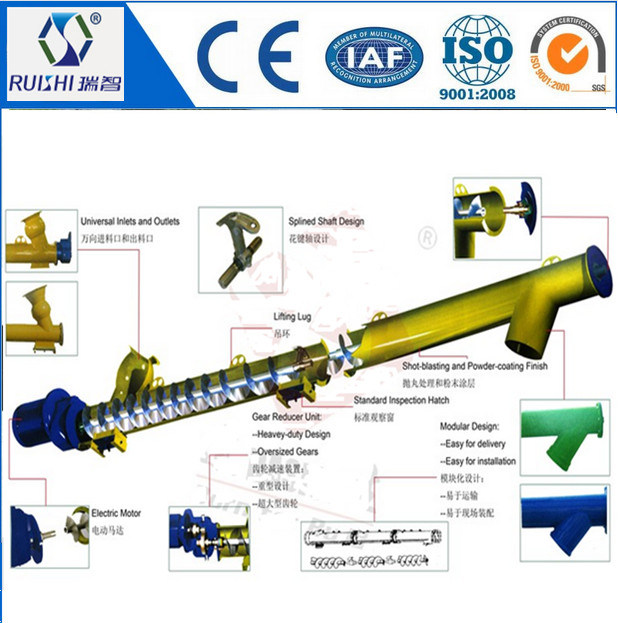
Working Principle:
Screw conveyor is relying on a spiral blade shaft in the trough of closed continuous rotation in order to impel the lose of material moving. At this time, the material are like the bolt, in spinning along the axial moving forward gradually, finally discharging mouth off.
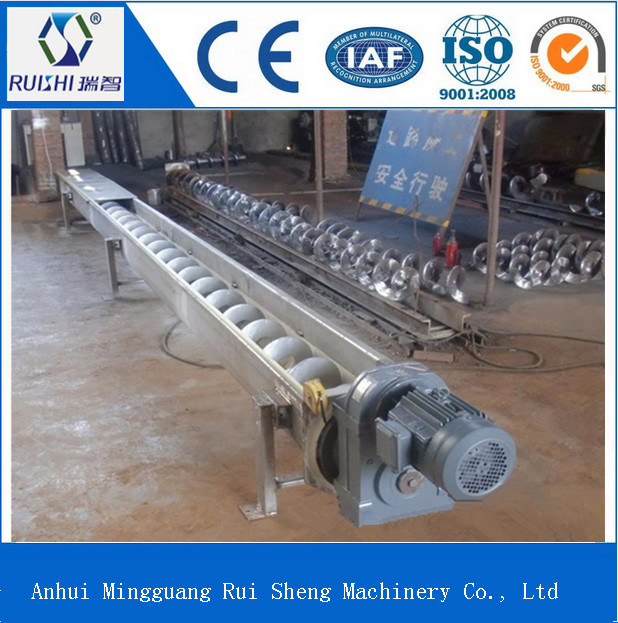
Quality Control:
1. Each machine is manufactured by professional experienced staff.
2. Production process is under strict supervision and adopts China and world toppest production engineering.
3. We offer one year guarantee for new machine since it leaves factory(within guarantee), Quick-wear part is excluded.we offer
free part and send it to you, you just pay the Express cost.
4. When warranty date expires, lifetime maintenance service is provided.
5. We always test the machine one by one, make sure it works well before leaves our factory.
6. any question, we will supply technical support and headling method or make a video show you when you need help.
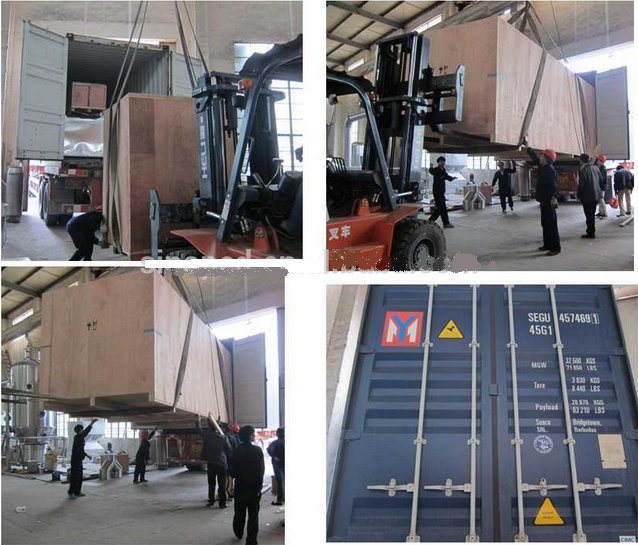
Why choose us:
We will provide you with the first-class technology, first-class products and first-class services to gain your recognition and trust:
1.Excellent manufacturing team with experience of nearly 15 years.
2.All can be customized to meet your needs&boost productivity.
3.Passed CE&ISO9001:2008 quality attestation.
4.Long-term cooperated transport company ensure the timely and safe delivery.
5.One-stop service save your precious time.
6.Save your purchasing time; Save your Quality Control cost; Save your transportation time and cost; Save your installation training cost.
The Die Castings that are created in this process can vary greatly in size and weight, ranging from a couple ounces to 100 pounds. One common application of die cast parts are housings - thin-walled enclosures, often requiring many ribs and bosses on the interior. Metal housings for a variety of appliances and equipment are often die cast. Several automobile components are also manufactured using die casting, including pistons, cylinder heads, and engine blocks. Other common die cast parts include propellers, gears, bushings, pumps, and Valves.
Die casting is a manufacturing process that can produce geometrically complex metal parts through the use of reusable molds, called dies. The die casting process involves the use of a furnace, metal, die casting machine, and die. The metal, typically a non-ferrous alloy such as aluminum or zinc, is melted in the furnace and then injected into the dies in the die casting machine. There are two main types of die casting machines - hot chamber machines (used for alloys with low melting temperatures, such as zinc) and cold chamber machines (used for alloys with high melting temperatures, such as aluminum). The differences between these machines will be detailed in the sections on equipment and tooling. However, in both machines, after the molten metal is injected into the dies, it rapidly cools and solidifies into the final part, called the casting. The steps in this process are described in greater detail in the next section.
Die cast parts can vary greatly in size and therefore require these measures to cover a very large range. As a result, die casting machines are designed to each accommodate a small range of this larger spectrum of values. Sample specifications for several different hot chamber and cold chamber die casting machines are given below.
Type | Clamp force (ton) | Max. shot volume (oz.) | Clamp stroke (in.) | Min. mold thickness (in.) | Platen size (in.) |
Hot chamber | 100 | 74 | 11.8 | 5.9 | 25 x 24 |
Hot chamber | 200 | 116 | 15.8 | 9.8 | 29 x 29 |
Hot chamber | 400 | 254 | 21.7 | 11.8 | 38 x 38 |
Cold chamber | 100 | 35 | 11.8 | 5.9 | 23 x 23 |
Cold chamber | 400 | 166 | 21.7 | 11.8 | 38 x 38 |
Cold chamber | 800 | 395 | 30 | 15.8 | 55 x 55 |
Cold chamber | 1600 | 1058 | 39.4 | 19.7 | 74 x 79 |
Cold chamber | 2000 | 1517 | 51.2 | 25.6 | 83 x 83 |
The selection of a material for die casting is based upon several factors including the density, melting point, strength, corrosion resistance, and cost. The material may also affect the part design. For example, the use of zinc, which is a highly ductile metal, can allow for thinner walls and a better surface finish than many other alloys. The material not only determines the properties of the final casting, but also impacts the machine and tooling. Materials with low melting temperatures, such as zinc alloys, can be die cast in a hot chamber machine. However, materials with a higher melting temperature, such as aluminum and copper alloys, require the use of cold chamber machine. The melting temperature also affects the tooling, as a higher temperature will have a greater adverse effect on the life of the dies.
Materials | Properties |
Aluminum alloys | ·Low density |
·Good corrosion resistance | |
·High thermal and electrical conductivity | |
·High dimensional stability | |
·Relatively easy to cast | |
·Requires use of a cold chamber machine | |
Copper alloys | ·High strength and toughness |
·High corrosion and wear resistance | |
·High dimensional stability | |
·Highest cost | |
·Low die life due to high melting temperature | |
·Requires use of a cold chamber machine | |
Zinc alloys | ·High density |
·High ductility | |
·Good impact strength | |
·Excellent surface smoothness allowing for painting or plating | |
·Requires such coating due to susceptibility to corrosion | |
·Easiest to cast | |
·Can form very thin walls | |
·Long die life due to low melting point | |
·Use of a hot chamber machine | |
Advantages: | ·Can produce large parts |
·Can form complex shapes | |
·High strength parts | |
·Very good surface finish and accuracy | |
·High production rate | |
·Low labor cost | |
·Scrap can be recycled |
Die Casting,Aluminum Die Casting,Die Casting Parts,Zinc Die Casting
Ningbo City Yinzhou Ruican Machinery Co.,Ltd , https://www.cnruican.com