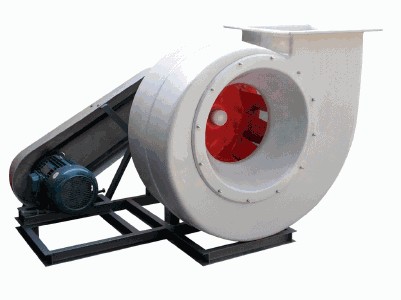
At present, with the rapid development of China's chemical industry, the use of composite materials to develop chemical industrial machinery production equipment has become the focus of many companies. However, how to solve the problems of high-pressure and air-tightness in chemical intermediate gas and exhaust gas purification processing equipment under special chemical process and complex medium environment has always been the key issue for the company. In this regard, Hebei Jiezhou Jiete Fiberglass Co., Ltd., with the assistance of scientific research and design units and large and medium-sized institutions, has been actively researching and succeeding. The new equipment not only achieves the purpose of anti-corrosion and sealing under complex media environment with excellent composite material properties, but also its excellent high-pressure resistance performance fundamentally improves the index requirements for the efficiency of the fan under the special chemical process conditions.
According to the person in charge of the company's research project, the product first fully utilized the corrosion resistance of the glass fiber reinforced plastic material, and through the change of the raw material process formula, effectively solved the problem of high pressure resistance, so that the equipment can withstand pressure up to 35000Pa and improve the pressure resistance coefficient by 10 times. . At the same time, through the technical innovation of the process structure such as the impeller axial width, suction surface thickness and meridian profile, the efficiency in the fan has reached over 85%. On this basis, through the development of the vacuum plus double-face sealing technology, the zero leakage of the media seal in the running state of the machine body is achieved, thereby reducing the corrosion of the machine body and the pollution to the working environment. This technology has obtained the national technical patent. At the same time, the application and improvement of new materials make the equipment not only have excellent explosion-proof functions, but also have a service life of more than 7 years, which greatly reduces the user's production cost.
At present, the company has invested nearly 10 million yuan to build two professional production lines. The products have achieved multiple specifications and varieties, and have produced an annual output of nearly 1,000 sets of production capacity.
The film output by the film output machine is a negative film that has formed a latent image of graphics and text. It must go through the processes of developing, fixing, and washing to make the negative of the graphic area and the blank area. This is the traditional process of making film. The process of developing and fixing can be done manually or by using a film developing machine. The film developing machine is composed of three tanks, and the film is drawn into the developing tank, fixing tank, and washing tank through the traction roller to complete the processing of the negative film in sequence.
film developing mchine, film washing machine
KC Printing Machine (Group) Limited , https://www.kcautopm.com