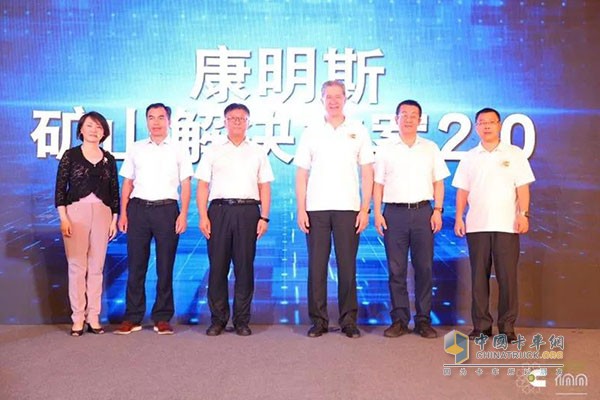
Li Xiao, general manager of Baotou Steel, Qi Qingfeng, general manager of Northern Shares, Steve Chapman, vice president of Cummins Group, Lin Jing, general manager of Cummins East Asia Distribution Division, and Xiang Yongdong, general manager of Cummins China Power Systems Division, etc. More than 100 people from both the media and the industry witnessed the event.
In the mining power market, Cummins serves global users with technological innovation and product reliability. In the history of Cummins's centuries, service mine customers have a history of more than 90 years. The mine has always been an important part of the Cummins business, with more than 28,000 engines and more than 3,700 technicians serving the world's mining customers worldwide. The mining market is also the starting point for Cummins China's business. In 1975, Cummins' first Chinese customer was Nanfen Iron Mine.
“Cummins has always adhered to the brand promise of continuous innovation and lifetime trust, providing customers with high-quality and reliable products, and building the benchmark power of mine application with excellent reliability, durability and performance advantages.†Cao Side said, “In order to Mine users provide faster and more efficient service support. Cummins became the first engine company to start a mine service to ensure that we can solve problems for users in the first time."
Steve Chapman, Vice President, Cummins Group
The cooperation between Cummins and Baotou Steel also has a long history, and business has been carried out since the 1980s. In 2019, in order to further enhance the all-round service support and effective control of the total life cycle cost (TCO), Baotou Steel Group and Cummins also reached a strategic partnership to promote the efficient attendance of mining equipment. Since the cooperation, there are data showing that Baotou Steel has achieved cost reduction and efficiency increase through overhaul workshop upgrade, super maintenance and Cummins parts procurement, which has extended the running time and reduced maintenance costs, labor costs and downtime from the root.
Yu Changzhi, deputy general manager of Baotou Steel Co., Ltd. said: "Since the signing of the strategic cooperation agreement, in the past few months, Cummins has effectively helped us to optimize from the entire life cycle of the equipment, truly reducing costs and increasing efficiency, the company zero The cost of components has been significantly reduced by 30%. We look forward to continuing our deepening cooperation with Cummins in the future and mutual benefit."
Cummins gives Baotou Holding a sincere cooperation and witness
The officially launched Cummins Mine Total Solution 2.0 will help customers further improve the efficient operation and service capacity of mining equipment. Lin Jing explained the value added by the program to the customer at the event site:
Through strategic linkage to ensure cooperation mechanisms, collaborative business objectives, and establish a high development direction in the industry;
Launched a comprehensive solution of TCO strategic guidance, helping customers improve through customized solutions such as mine digital operation efficiency monitoring, forward-looking service solutions, overhaul value package, value-added maintenance package, preheating system solution, and oil real-time analysis. Equipment operation efficiency, improve maintenance quality, and strengthen risk control;
Implement improvement plans supported by technical experts to help customers improve their self-study technical capabilities, upgrade production assembly processes, improve quality control standards and systems, improve maintenance and repair quality, and reduce operating costs throughout the life cycle of equipment;
Cummins also provides professional and close-knit service support, responding quickly to customer needs and equipment operation and maintenance, and helping customers improve equipment operation and management efficiency through new products, new technologies, new standards and new processes.
Participating leaders to observe the Cummins mine engine
Cummins has always adhered to the customer-centric philosophy, in order to better close to and serve end customers, Cummins further optimized China's mine service resources in 2019. Cummins' presence in more than 30 mines across the country's mine service team and a team of experts who integrate global mine service experience and understand the specific needs of Chinese mine users are the strength of Cummins 2.0 solutions.
Based on the concept of mine life cycle cost, they provide customers with the most cost-effective, customized and competitive value packages and support solutions to ensure the efficient operation of equipment and provide a series of value-added services for mine customers.
The overall mine solution 2.0 is a manifestation of Cummins' centuries-old accumulation and a solid commitment of Cummins to Chinese users. Taking Cummins stationed mine service as an example, no matter how bad the environment is, Cummins' first-line resident staff are sticking to their posts and actively responding to customer needs. From the cold Tibetan plateau to the northwest hinterland of the wind and sand, there are footprints of resident service personnel everywhere. They are far away from home to the mining area and provide strong service support for the normal operation of the equipment.
At this meeting, a number of excellent mining service personnel won the "Service Artisan Award", with the exquisite skills, professional service capabilities, caring customer care to prove to the mine customers, Cummins engine, trustworthy!
A number of excellent mine service personnel received the "Service Craftsman Award"
The launch of Cummins Mine Solutions 2.0 is also inseparable from the support of OEM customers. In the more than 40 years of entering China, Cummins has strengthened cooperation with North China, Komatsu and other excellent OEMs, chained superior resources, improved life cycle solutions, and jointly built high-quality products and services to mine customers and won the support of customers. And trust.
As the other host of Baotou Station - the North shares, and Cummins has been consistent with the Cummins engine for more than 30 years. Highly recognized for the performance and service support of Cummins engines. The Cummins Power North stock equipment is widely used in major mining areas in the north and south of China. With the deepening of the market strategy of the Northern Region's expansion of the Belt and Road, the two companies have achieved win-win results in the global market.
Cummins gives North Holdings a win-win cooperation witness
Qi Qingfeng, general manager of the Northern Shares, congratulated Cummins on his 100th birthday and also expressed great hopes for the further development of the future cooperation between the two companies: "At the same time as the domestic market is successful, we are also expanding overseas markets. Our cooperation with Cummins has Expanding to the world. In the future, both parties will continue to strengthen cooperation in the field of intelligent monitoring such as remote monitoring and data analysis, and promote the development and cooperation of both sides in the direction of smart mines."
Reading volume: Source: Cummins China Author: No QFood Additive,Ws-5 Cooling Agent,Ws-23 Powder,Chiller Cooling Additive
XI'AN TAIMA BIOLOGICAL ENGINEERING CO.LTD , https://www.taimabio.com