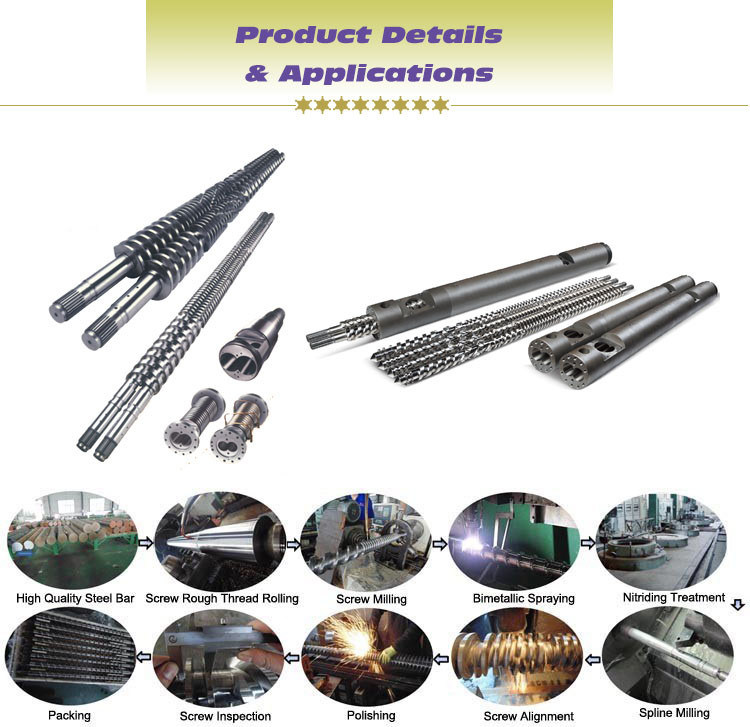
Technical Information for Conical Twin Screw Barrel | |||
Main Base materials | 1.38CrMoAlA (SACM645) | Main Alloy Materials | 1. Ni-based alloy/Deloro alloy |
2. SKD-61 (Special Tool Steel) | 2. Tungsten carbide/Wolfram carbide | ||
3. 42CrMo (Ultrahigh StrengthSteel) | 3. NiCo-based alloy | ||
4. DC53 (Cold WorkDie Steel) | 4. Fe-based alloy | ||
5. W6Mo5Cr4V2 (High-SpeedToolSteel) | 5. Co-based alloy | ||
Processing Technics | 1. Heat treatment | Technical parameters | Nitriding layer depth:0.5-0.8mm |
2. Quenching | Nitrided hardness:900-1000HV | ||
3. Nitriding treatment | Bimetallic layer depth:3 mm | ||
4. Bimetallic alloy welding for screw | Bimetallic hardness:57~69HRC | ||
5. Bimetallic alloy centrifugal casting for barrel | Hard-chrome plating hardness after nitriding:≥950HV | ||
6. Hard-chrome electroplating | Chrome-plating layer depth:0.03-0.09mm | ||
Linearity of screw:0.015mm | Surface roughness:Ra 0.4 |
The most common types of conical twin screw barrel extruder | |||
types of screw (d/D) | length of work(mm) | quantity ofextruder(kg/h) | speed of screw rotate(rpm) |
Φ35/77 | 810 | 40-70 | 5~50 |
Φ45/99 | 990 | 50-80 | 5~45 |
Φ51/105 | 1070 | 100-150 | 4~45 |
Φ51/105 | 1220 | 100-150 | 4~45 |
Φ55/110 | 1220 | 120-180 | 4~40 |
Φ60/125 | 1320 | 150-200 | 4~40 |
Φ65/120 | 1440 | 200-250 | 4~40 |
Φ65/132 | 1440 | 200-250 | 4~40 |
Φ70/140 | 1460 | 220-300 | 4~40 |
Φ75/150 | 1480 | 250-320 | 4~35 |
Φ80/143 | 1660 | 300-360 | 4~35 |
Φ80/156 | 1800 | 300-360 | 4~35 |
Φ90/184 | 2000 | 400-500 | 3~35 |
The most common types of parallel twin screw barrel extruder | ||||||
D35/5 | D45/2 | D50/2 | D60/2 | D65/2 | D70/2Â Â | D72/2 |
D75/2 | D80/2 | D85/2 | D90/2 | D93/2 | D100/2 | D105/2 |
D110/2 | D115/2 | D120/2 | D125/2 | D130/2 | D140/2 | D150/2 |
D160/2 | D170/2 | D180/2 | D190/2 | D200/2 | D200/2 | D250/2 |
Screw types:
Gradual change, chop, barrier, distributary, separate, air exhausting, pin, mixing and etc.
For good plasticizing effect, we have different design of screw barrel to meet customer's demand.
Specification :
Dia 20mm-250mm; L/D=15-45
Scope of Application:
1. Generally plastic material
2. Pipe/ Profile/ Sheet/Pelletizing
3. WPC, ABS, TPR, TPU, PMMA, C-PVC, UPVC, RPVC, PET, EVA, PU,PE etc
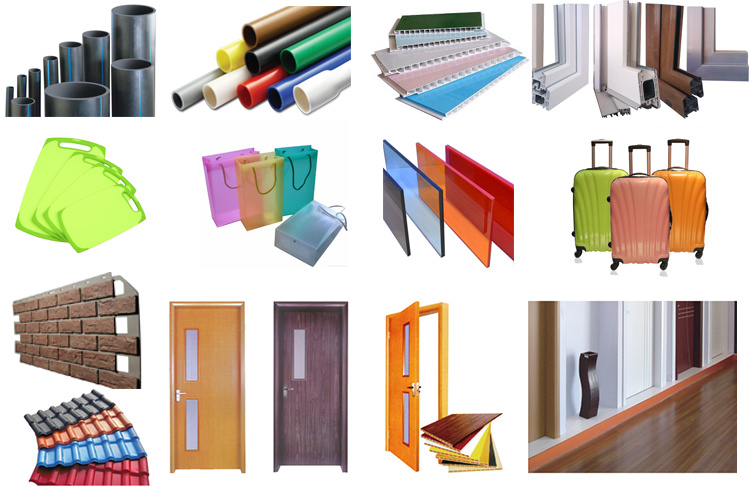
Treatment:
Nitrized, Chrome coating, Quenching, Bimetallic
We are foucs on each process to make sure each screw barrel is qualified according to technical requirement.Â
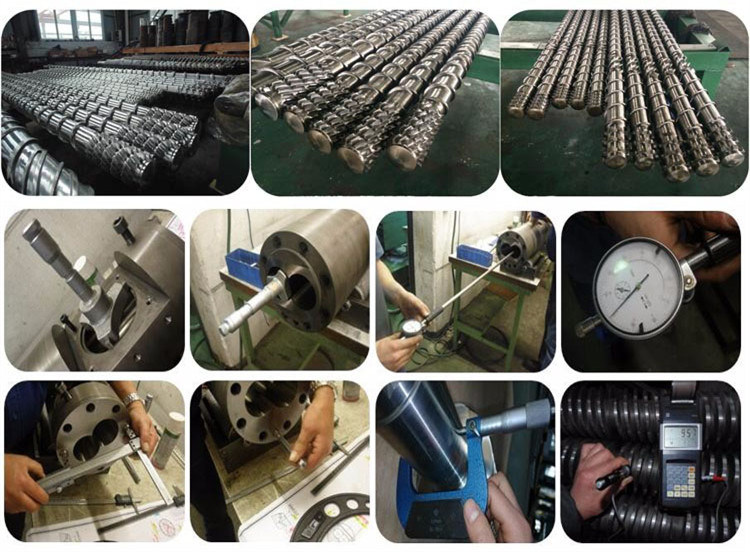
Packaging Details:
1. Be brushed anti-corrosive oil on extruder machine single screw.Â
2. Packed with film.Â
3. Packed in the AA wooden.
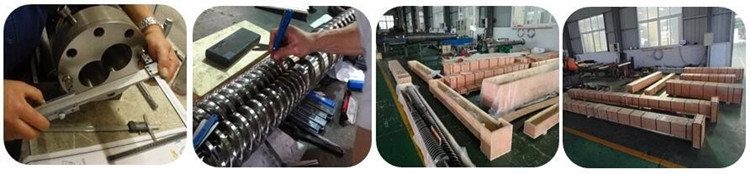

Please provide samples or requirements about dimensions and tolerances of , semi-finished and Finished Products, the equipment, the monthlly comsumption quantity, the current screw and barrel you are using, HRC and so on.
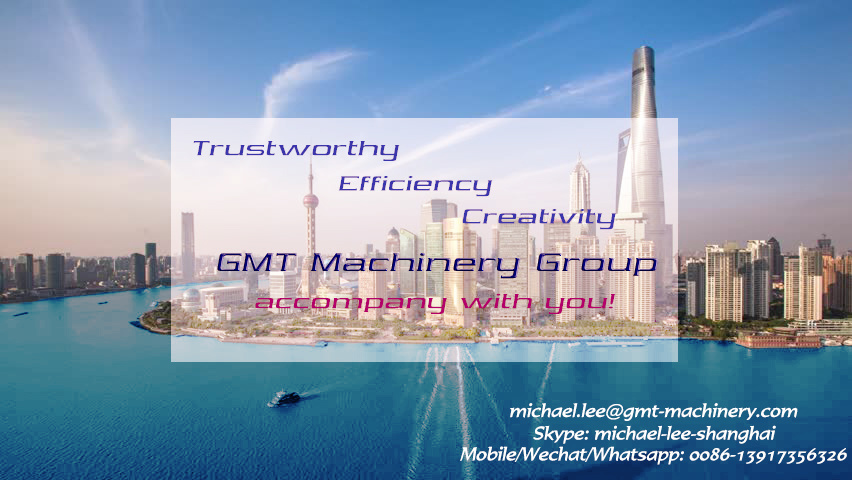
For more information, please kindly contact as below:
Mobile: 0086-13917356326
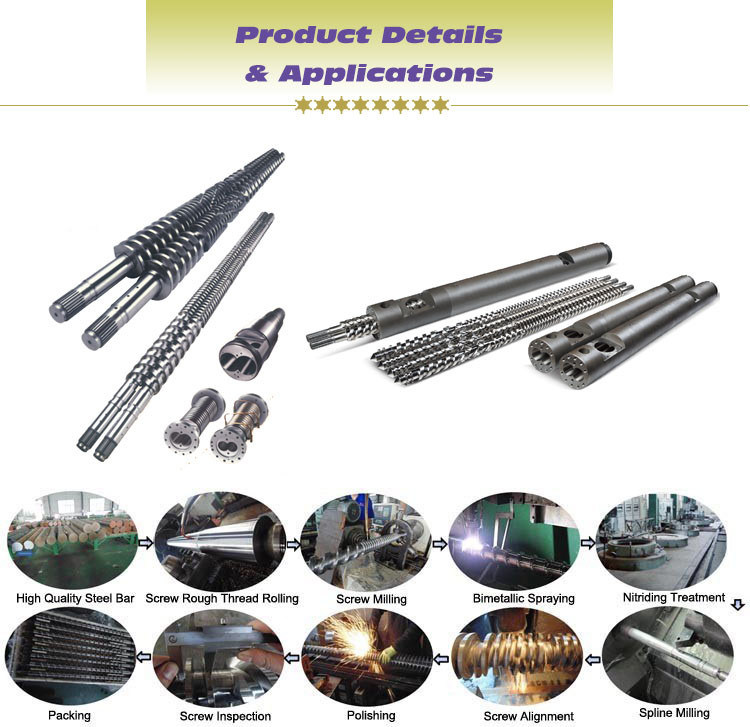
Technical Information for Conical Twin Screw Barrel | |||
Main Base materials | 1.38CrMoAlA (SACM645) | Main Alloy Materials | 1. Ni-based alloy/Deloro alloy |
2. SKD-61 (Special Tool Steel) | 2. Tungsten carbide/Wolfram carbide | ||
3. 42CrMo (Ultrahigh StrengthSteel) | 3. NiCo-based alloy | ||
4. DC53 (Cold WorkDie Steel) | 4. Fe-based alloy | ||
5. W6Mo5Cr4V2 (High-SpeedToolSteel) | 5. Co-based alloy | ||
Processing Technics | 1. Heat treatment | Technical parameters | Nitriding layer depth:0.5-0.8mm |
2. Quenching | Nitrided hardness:900-1000HV | ||
3. Nitriding treatment | Bimetallic layer depth:3 mm | ||
4. Bimetallic alloy welding for screw | Bimetallic hardness:57~69HRC | ||
5. Bimetallic alloy centrifugal casting for barrel | Hard-chrome plating hardness after nitriding:≥950HV | ||
6. Hard-chrome electroplating | Chrome-plating layer depth:0.03-0.09mm | ||
Linearity of screw:0.015mm | Surface roughness:Ra 0.4 |
The most common types of conical twin screw barrel extruder | |||
types of screw (d/D) | length of work(mm) | quantity ofextruder(kg/h) | speed of screw rotate(rpm) |
Φ35/77 | 810 | 40-70 | 5~50 |
Φ45/99 | 990 | 50-80 | 5~45 |
Φ51/105 | 1070 | 100-150 | 4~45 |
Φ51/105 | 1220 | 100-150 | 4~45 |
Φ55/110 | 1220 | 120-180 | 4~40 |
Φ60/125 | 1320 | 150-200 | 4~40 |
Φ65/120 | 1440 | 200-250 | 4~40 |
Φ65/132 | 1440 | 200-250 | 4~40 |
Φ70/140 | 1460 | 220-300 | 4~40 |
Φ75/150 | 1480 | 250-320 | 4~35 |
Φ80/143 | 1660 | 300-360 | 4~35 |
Φ80/156 | 1800 | 300-360 | 4~35 |
Φ90/184 | 2000 | 400-500 | 3~35 |
The most common types of parallel twin screw barrel extruder | ||||||
D35/5 | D45/2 | D50/2 | D60/2 | D65/2 | D70/2Â Â | D72/2 |
D75/2 | D80/2 | D85/2 | D90/2 | D93/2 | D100/2 | D105/2 |
D110/2 | D115/2 | D120/2 | D125/2 | D130/2 | D140/2 | D150/2 |
D160/2 | D170/2 | D180/2 | D190/2 | D200/2 | D200/2 | D250/2 |
Screw types:
Gradual change, chop, barrier, distributary, separate, air exhausting, pin, mixing and etc.
For good plasticizing effect, we have different design of screw barrel to meet customer's demand.
Specification :
Dia 20mm-250mm; L/D=15-45
Scope of Application:
1. Generally plastic material
2. Pipe/ Profile/ Sheet/Pelletizing
3. WPC, ABS, TPR, TPU, PMMA, C-PVC, UPVC, RPVC, PET, EVA, PU,PE etc
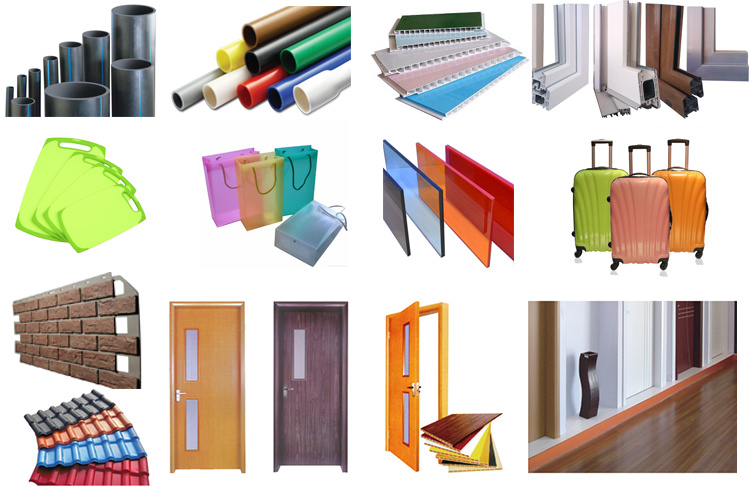
Treatment:
Nitrized, Chrome coating, Quenching, Bimetallic
We are foucs on each process to make sure each screw barrel is qualified according to technical requirement.Â
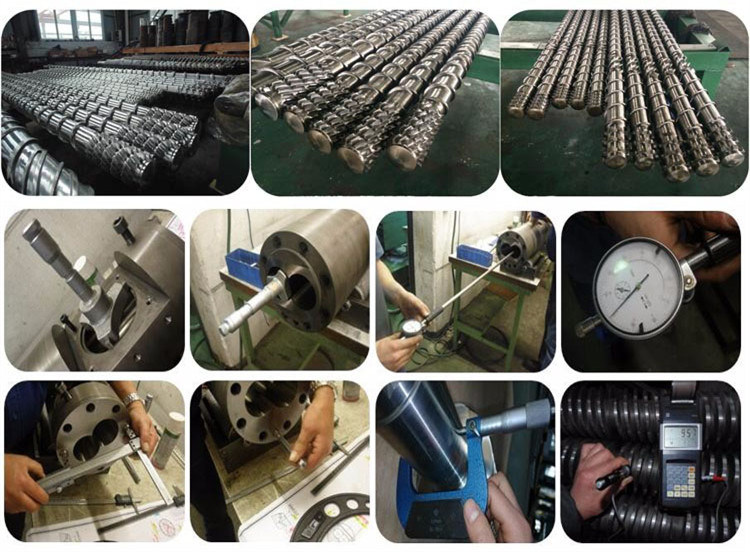
Packaging Details:
1. Be brushed anti-corrosive oil on extruder machine single screw.Â
2. Packed with film.Â
3. Packed in the AA wooden.
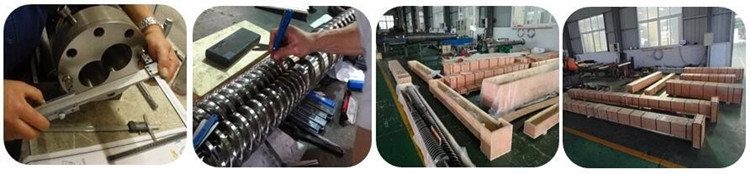

Please provide samples or requirements about dimensions and tolerances of , semi-finished and finished products, the equipment, the monthlly comsumption quantity, the current screw and barrel you are using, HRC and so on.
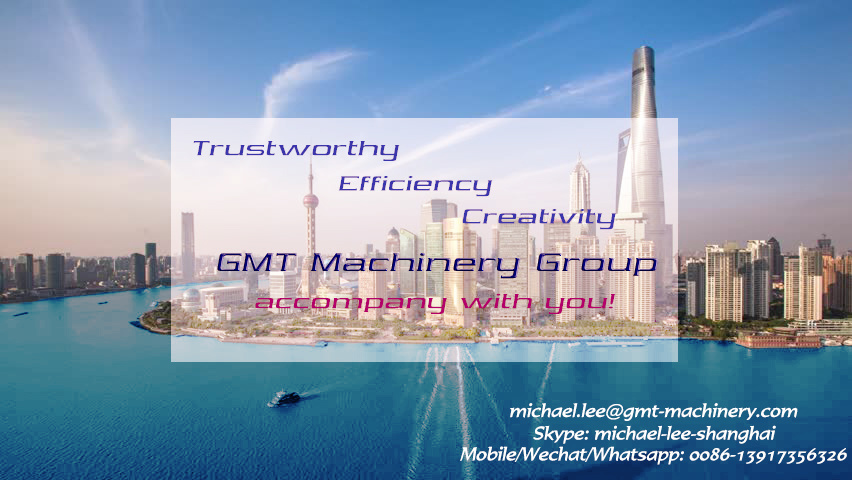
For more information, please kindly contact as below:
Mobile: 0086-13917356326
Deep drawing is one of the most popular metal forming process of forming blank sheets of metal into a desired shape. Equipped with deep draw presses range in tonnage capacity from 5 to 350 tons, MSG` deep drawn presses are capable of deep drawing various metal types with material thicknesses from 0.2mm - 6mm, part diameters from 2mm - 900mm, and lengths up to 1000mm.
Deep drawing process provides better strength properties, seamless structure, consistency on the finished parts, and it is especially beneficial when producing high volumes. The process is also recommended for product geometries that are unachievable through other manufacturing methods. Deep drawn products are of all shapes and sizes, such as assembly housings, kettles, cans, cookware, and kitchen sinks. MSG`s engineers prepare metal blanks in advance of the deep drawing process to ensure that the finished parts are free from tears and imperfections.
Deep Drawing,Stock Pot,Milk Bucket,Deep Draw Stamping
Huiye Hardware & Electrical Equipment Company Ltd. , https://www.hardwarehuiye.com