Overview Huaibei Power Plant #4 unit is a 125MW unit put into production in September 1977. The boiler is a coal-fired ultra-high pressure, intermediate reheating natural circulation drum boiler. The steam turbine is an ultra-high pressure, double-cylinder, and double-discharge steam condensing unit. The three main aircrafts are manufactured by the three major OEMs in Shanghai.
First, the transformation of the unit before the operation of the situation Huaibei Power Plant # 4 units in the 70s put into operation centralized control of coal-fired units, thermal control equipment is outdated, control room design station screen 11, 5 console, and another zero meters There are water supply chambers and division mill rooms on the floor, with more operating equipment, more operators, more labor intensity, larger equipment maintenance, more spare parts for use, and thermal control instruments are mostly old type II with low degree of automation. Feed water and feed powder, shaft seal pressure automatic adjustment system put into operation. Some protection systems cannot be put into operation due to equipment. Moreover, with the improvement of thermal control instrumentation technology and the automation level of power plants, especially the requirements of primary frequency modulation and AGC, the existing conventional control instruments are far from meeting the requirements for safe and reliable economic operation and on-line state analysis of the unit.
Second, the determination of the transformation program In view of the above reasons, the provincial company decided to carry out transformation of DCS, DEH integrated control of # 4 units, after careful selection,
It is determined that the DCS control part uses XDPS-400 system of Xinhua Engineering Control Co., Ltd. and DEH adopts Xinhua's DEH-IIIA system. The scope of DCS retrofit covers machine and furnace control, electrical auxiliary machine control, and electrical analog and electrical switch status acquisition. The system is divided into DAS, SCS, MCS, and FSSS. The DEH system includes turbine control, overspeed protection, and turbine protection system (ETS). A total of 4 operator stations, 2 engineer stations, 1 historical station, 1 gateway, 16 control stations, more than 2600 points. System configuration and communication network are as follows:
The I/O station and the DPU communicate with each other through the switch, changing the previous bus communication method.
1. The DAS system includes the collection and processing of all main and auxiliary engines such as pressure and temperature signals (the auxiliary machine current signal takes into account the integrity of the system.
Enter the SCS system). The DAS system has the following functions:
◠Display of current values ​​and status of all parameters of the unit;
â— All parameters of the unit alarm, record, prompt and print;
â— Real-time curve display and printing of main parameters;
â— SOE point recording, prompting and printing;
â— history and curve of all parameters;
â— accident recall and printing;
â— Report generation and printing;
â— Second calculation.
â— Voice alarm function â— Graphic trigger function 2. The original fire-extinguishing protection host is removed from the FSSS system, and 12 flame signals are directly passed through the mV signal acquisition terminal board to enter two pieces of card processing for flame monitoring and furnace fire-free judgment, and the danger is performed. Decentralized, piloted blower shutdown, and hearth pressure signals were all hazard-distributed. The FSSS system is designed for furnace fire protection, main fuel loss, furnace pressure protection, blower fan tripping and drum water level protection (logic part), first-out reason memory, combustion instability alarm, furnace pressure alarm, furnace purge management and fuel oil Control and high-energy ignition system control and other functions, to achieve the furnace combustion control and management.
3, SCS system SCS system covers the start and stop control of the auxiliary machine of the boiler, the control and interlock protection of the electric door and the remote operation door. The program control logic has designed the step display, step-by-step and fault alarm functions. Trip is automatically determined by the device control module. The main functions are as follows:
â—Auxiliary machine interlocking protection interlocking protection function for the machine-side double auxiliary machine and boiler large interlock â—Automatic start-stop control for the pulverizer â—No oil flow protection for the pulverizer â—Program control for the fixed-discharge system â—Start-stop procedure for the auxiliary machine Control â—Adjustment and control of remote operation door and electric door â—Powder system program control â—Deaerator water level protection â—High water level protection â—Feed pump protection â—Steam bypass protection 4ã€MCS system MCS system has a total of 21 sets of automatic adjustment system The process variables used are averaged out of three or two, and are collected by different card pieces. Each loop control card only collects the relevant process quantity related to the loop adjustment, reduces the number of sampling points of the card, and ensures the calculation speed of the loop. . All automatic systems can achieve hand/automatic bumpless switching. The specific design features are as follows:
â— AGC and primary frequency modulation realize the automatic load-reduction load control and primary frequency modulation function of the unit through the telecontrol system.
â— Coordinated Control (CCS)
LMCC (Load Management Center)
According to the unit operating status, select different load instructions, the load command has the highest change rate, the lowest load rejection protection, the manual reference load instruction, and the furnace control system completes the coordination between the furnaces according to the LMCC command signal. There are four modes of operation:
Machine-cooker coordinated control mode Steam turbine basic mode Boiler basic mode Manual control mode According to the unit's constant pressure and sliding pressure start-up, operation mode and load instruction, the pre-press pressure setting is given, and the pressure change rate is limited to realize various operation modes. Disturbance switching â—Automatic water level adjustment for water supply automatic drums is performed with a signal in the middle of the three acquisitions, and the water level protection water level signal for the drums is rigorously applied as required to obtain three, two, two, one, or one treatment. â— One or two desuperheating water controls , Reheater spray adjustment â— Automatic coal feeder level â— Deaerator pressure automatic â— Deaerator water level automatic â— High and middle cylinder seal pressure automatic, low pressure cylinder seal pressure automatic â— Continuous row expansion container level automatic â— Condenser water level conversion is automatic because the condenser water level measurement is a negative pressure system. For safety reasons, the condenser water level electrical contact table alarm output is used as a confirmation of the condenser water level adjustment signal. 5. DEH system DEH adopts high voltage pure electricity. Tuning, turbine protection (ETS) and overspeed trip together constitute the AST (automatic shutdown) logic loop.
â— The DEH system is relatively independent and complete, the required signals are directly entered into the DEH cabinet, and then broadcast to the Internet through the DPU of the DEH system. The DEH system is only used as a station of the complete DCS. â— The DEH is connected to the electrical synchronization device and the MCS system through hard wiring. Completion of quasi-synchronous phase adjustment of turbine speed, generator grid-connected and unit-input coordinated control (including AGC and primary frequency modulation) Control of unit power and turbine speed by CCS system when DEH is in remote control â— ETS
After the retrofitting, the relay circuit of the original turbine protection is canceled, and the danger, alarm protection signal, analog monitor signal of the special measurement system device of Philip and the hard contact signal of the special measurement probe and the contact signal of the protection switching disc are directly connected to the DEH cabinet. The LPC terminal board outputs the tripping signal after logical operation of the redundant 3 pairs of LPC cards, and is also collected by the DPU to broadcast to the Internet to become a global point. The LPC card is used in place of the commonly used PLC to make the system structure complete and unified, and the clock is unified. , Signal memory is complete, easy to maintain â— Because each station DPU load rate is small (less than 30%) and the system network communication speed is very fast, so the signal contact between DCS systems in addition to CCS and DEH, DEH and automatic quasi synchronization device In addition to hard wiring, all other data sharing is achieved through Internet communication. 1. After transformation project construction and transformation, the project was completed through a joint conference and a second meeting held by the power plant, Xinhua company, and the provincial pilot plant after determining the transformation plan. DCS,
DEH transformation of the hardware configuration and system design. After that, we carried out serious preparatory work before major overhauls. Through on-site investigation and discussion and design, we formulated the overall plan and specific implementation plan for the construction of the DCS and DEH rebuilding thermal control system for the overhaul of the unit, and compiled the overhaul instruction manual and the detailed timetable decomposition table. And equipment operation debugging list.
1, Taiwan screen and other transformation due to the longer life of the original cable, and many signal cables for ordinary cables, inconsistent with the shielding requirements, decided to replace all. The old cable trays were reconstructed and 60,000 meters of new cables were all layered and tiled. They were laid in strict accordance with the design requirements. The transformed screen is four consoles and two vertical screens. On the console, except the CRT and DEH keyboards, only the sound and light alarm test silence button and two manual MFT buttons and fuel pump control buttons are retained; the screen retains Drum water level and flame industrial TV, steam drum water level, condenser water level, deaerator water level electrical contact, turbine speed, generator active, generator leakage meter, control and acousto-optic to the powder power supply and AC/DC oil pump Alarm row, turbine switch protection switch and coal controller. The control room is concise and clear, giving the operating staff a very easy working environment.
2. After the system is commissioned and put into operation, after the system is powered on, the network is restored and the copying machine is in progress, due to the full preparation of the preliminary preparation, the operation and configuration of the XDPS-400 system is very flexible and convenient. DCS and DEH systems The dynamic alignment with the thermal control system took only 12 days to complete smoothly.
Since the unit was officially put into operation on June 11, 2002, the DCS and DEH systems have been operating stably. The MCS systems, such as the AGC and primary frequency modulation, as well as the protection and interlocking circuits have all been put into operation and are in good operation. There has been no abnormality in the integrated system. It provides a good guarantee for the safe operation of the unit, and at the same time greatly improves the automation level and economy of the unit operation, realizes the automation of load dispatching, and greatly reduces the labor intensity of the operating personnel.
The operation and configuration of the XDPS-400 DCS system is very flexible and convenient. The DPU configuration can be modified and downloaded online. The configuration diagram is a SAMA diagram and can be displayed online. All DPU configurations can be performed online, which gives heat. Control system maintenance brings great convenience, and it is also unmatched by other DCS systems. But at the same time, it is the flexibility of on-line modification of the configuration, that is, the change is effective, especially the DEH system configuration modification may directly affect the safe operation of the unit, there is a great danger, which is also the thermal control maintenance personnel Put forward higher requirements. On the one hand, we must improve the technical level and operational rigor of DCS system maintenance personnel. At the same time, we must strengthen the management of DCS systems and establish strict rules and regulations for operation and approval so that we can better use XDPS. The superiority of the -400 DCS system.
First, the transformation of the unit before the operation of the situation Huaibei Power Plant # 4 units in the 70s put into operation centralized control of coal-fired units, thermal control equipment is outdated, control room design station screen 11, 5 console, and another zero meters There are water supply chambers and division mill rooms on the floor, with more operating equipment, more operators, more labor intensity, larger equipment maintenance, more spare parts for use, and thermal control instruments are mostly old type II with low degree of automation. Feed water and feed powder, shaft seal pressure automatic adjustment system put into operation. Some protection systems cannot be put into operation due to equipment. Moreover, with the improvement of thermal control instrumentation technology and the automation level of power plants, especially the requirements of primary frequency modulation and AGC, the existing conventional control instruments are far from meeting the requirements for safe and reliable economic operation and on-line state analysis of the unit.
Second, the determination of the transformation program In view of the above reasons, the provincial company decided to carry out transformation of DCS, DEH integrated control of # 4 units, after careful selection,
It is determined that the DCS control part uses XDPS-400 system of Xinhua Engineering Control Co., Ltd. and DEH adopts Xinhua's DEH-IIIA system. The scope of DCS retrofit covers machine and furnace control, electrical auxiliary machine control, and electrical analog and electrical switch status acquisition. The system is divided into DAS, SCS, MCS, and FSSS. The DEH system includes turbine control, overspeed protection, and turbine protection system (ETS). A total of 4 operator stations, 2 engineer stations, 1 historical station, 1 gateway, 16 control stations, more than 2600 points. System configuration and communication network are as follows:
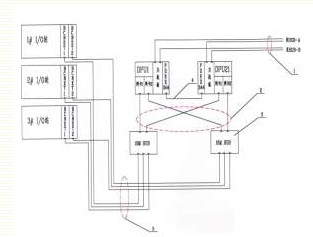
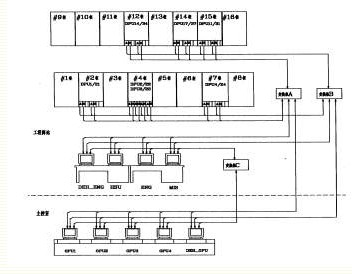
Enter the SCS system). The DAS system has the following functions:
◠Display of current values ​​and status of all parameters of the unit;
â— All parameters of the unit alarm, record, prompt and print;
â— Real-time curve display and printing of main parameters;
â— SOE point recording, prompting and printing;
â— history and curve of all parameters;
â— accident recall and printing;
â— Report generation and printing;
â— Second calculation.
â— Voice alarm function â— Graphic trigger function 2. The original fire-extinguishing protection host is removed from the FSSS system, and 12 flame signals are directly passed through the mV signal acquisition terminal board to enter two pieces of card processing for flame monitoring and furnace fire-free judgment, and the danger is performed. Decentralized, piloted blower shutdown, and hearth pressure signals were all hazard-distributed. The FSSS system is designed for furnace fire protection, main fuel loss, furnace pressure protection, blower fan tripping and drum water level protection (logic part), first-out reason memory, combustion instability alarm, furnace pressure alarm, furnace purge management and fuel oil Control and high-energy ignition system control and other functions, to achieve the furnace combustion control and management.
3, SCS system SCS system covers the start and stop control of the auxiliary machine of the boiler, the control and interlock protection of the electric door and the remote operation door. The program control logic has designed the step display, step-by-step and fault alarm functions. Trip is automatically determined by the device control module. The main functions are as follows:
â—Auxiliary machine interlocking protection interlocking protection function for the machine-side double auxiliary machine and boiler large interlock â—Automatic start-stop control for the pulverizer â—No oil flow protection for the pulverizer â—Program control for the fixed-discharge system â—Start-stop procedure for the auxiliary machine Control â—Adjustment and control of remote operation door and electric door â—Powder system program control â—Deaerator water level protection â—High water level protection â—Feed pump protection â—Steam bypass protection 4ã€MCS system MCS system has a total of 21 sets of automatic adjustment system The process variables used are averaged out of three or two, and are collected by different card pieces. Each loop control card only collects the relevant process quantity related to the loop adjustment, reduces the number of sampling points of the card, and ensures the calculation speed of the loop. . All automatic systems can achieve hand/automatic bumpless switching. The specific design features are as follows:
â— AGC and primary frequency modulation realize the automatic load-reduction load control and primary frequency modulation function of the unit through the telecontrol system.
â— Coordinated Control (CCS)
LMCC (Load Management Center)
According to the unit operating status, select different load instructions, the load command has the highest change rate, the lowest load rejection protection, the manual reference load instruction, and the furnace control system completes the coordination between the furnaces according to the LMCC command signal. There are four modes of operation:
Machine-cooker coordinated control mode Steam turbine basic mode Boiler basic mode Manual control mode According to the unit's constant pressure and sliding pressure start-up, operation mode and load instruction, the pre-press pressure setting is given, and the pressure change rate is limited to realize various operation modes. Disturbance switching â—Automatic water level adjustment for water supply automatic drums is performed with a signal in the middle of the three acquisitions, and the water level protection water level signal for the drums is rigorously applied as required to obtain three, two, two, one, or one treatment. â— One or two desuperheating water controls , Reheater spray adjustment â— Automatic coal feeder level â— Deaerator pressure automatic â— Deaerator water level automatic â— High and middle cylinder seal pressure automatic, low pressure cylinder seal pressure automatic â— Continuous row expansion container level automatic â— Condenser water level conversion is automatic because the condenser water level measurement is a negative pressure system. For safety reasons, the condenser water level electrical contact table alarm output is used as a confirmation of the condenser water level adjustment signal. 5. DEH system DEH adopts high voltage pure electricity. Tuning, turbine protection (ETS) and overspeed trip together constitute the AST (automatic shutdown) logic loop.
â— The DEH system is relatively independent and complete, the required signals are directly entered into the DEH cabinet, and then broadcast to the Internet through the DPU of the DEH system. The DEH system is only used as a station of the complete DCS. â— The DEH is connected to the electrical synchronization device and the MCS system through hard wiring. Completion of quasi-synchronous phase adjustment of turbine speed, generator grid-connected and unit-input coordinated control (including AGC and primary frequency modulation) Control of unit power and turbine speed by CCS system when DEH is in remote control â— ETS
After the retrofitting, the relay circuit of the original turbine protection is canceled, and the danger, alarm protection signal, analog monitor signal of the special measurement system device of Philip and the hard contact signal of the special measurement probe and the contact signal of the protection switching disc are directly connected to the DEH cabinet. The LPC terminal board outputs the tripping signal after logical operation of the redundant 3 pairs of LPC cards, and is also collected by the DPU to broadcast to the Internet to become a global point. The LPC card is used in place of the commonly used PLC to make the system structure complete and unified, and the clock is unified. , Signal memory is complete, easy to maintain â— Because each station DPU load rate is small (less than 30%) and the system network communication speed is very fast, so the signal contact between DCS systems in addition to CCS and DEH, DEH and automatic quasi synchronization device In addition to hard wiring, all other data sharing is achieved through Internet communication. 1. After transformation project construction and transformation, the project was completed through a joint conference and a second meeting held by the power plant, Xinhua company, and the provincial pilot plant after determining the transformation plan. DCS,
DEH transformation of the hardware configuration and system design. After that, we carried out serious preparatory work before major overhauls. Through on-site investigation and discussion and design, we formulated the overall plan and specific implementation plan for the construction of the DCS and DEH rebuilding thermal control system for the overhaul of the unit, and compiled the overhaul instruction manual and the detailed timetable decomposition table. And equipment operation debugging list.
1, Taiwan screen and other transformation due to the longer life of the original cable, and many signal cables for ordinary cables, inconsistent with the shielding requirements, decided to replace all. The old cable trays were reconstructed and 60,000 meters of new cables were all layered and tiled. They were laid in strict accordance with the design requirements. The transformed screen is four consoles and two vertical screens. On the console, except the CRT and DEH keyboards, only the sound and light alarm test silence button and two manual MFT buttons and fuel pump control buttons are retained; the screen retains Drum water level and flame industrial TV, steam drum water level, condenser water level, deaerator water level electrical contact, turbine speed, generator active, generator leakage meter, control and acousto-optic to the powder power supply and AC/DC oil pump Alarm row, turbine switch protection switch and coal controller. The control room is concise and clear, giving the operating staff a very easy working environment.
2. After the system is commissioned and put into operation, after the system is powered on, the network is restored and the copying machine is in progress, due to the full preparation of the preliminary preparation, the operation and configuration of the XDPS-400 system is very flexible and convenient. DCS and DEH systems The dynamic alignment with the thermal control system took only 12 days to complete smoothly.
Since the unit was officially put into operation on June 11, 2002, the DCS and DEH systems have been operating stably. The MCS systems, such as the AGC and primary frequency modulation, as well as the protection and interlocking circuits have all been put into operation and are in good operation. There has been no abnormality in the integrated system. It provides a good guarantee for the safe operation of the unit, and at the same time greatly improves the automation level and economy of the unit operation, realizes the automation of load dispatching, and greatly reduces the labor intensity of the operating personnel.
The operation and configuration of the XDPS-400 DCS system is very flexible and convenient. The DPU configuration can be modified and downloaded online. The configuration diagram is a SAMA diagram and can be displayed online. All DPU configurations can be performed online, which gives heat. Control system maintenance brings great convenience, and it is also unmatched by other DCS systems. But at the same time, it is the flexibility of on-line modification of the configuration, that is, the change is effective, especially the DEH system configuration modification may directly affect the safe operation of the unit, there is a great danger, which is also the thermal control maintenance personnel Put forward higher requirements. On the one hand, we must improve the technical level and operational rigor of DCS system maintenance personnel. At the same time, we must strengthen the management of DCS systems and establish strict rules and regulations for operation and approval so that we can better use XDPS. The superiority of the -400 DCS system.
Speciality Silicones,Linear Polysiloxane Compounds,Silicone Oil For Treadmill,Silicone Oil For Lubricant
Henan Minmetals East New Materials CO. LTD. , https://www.silicon-materials.com